In the fall of 2015, Professors Ila Berman and DataLab (Mona El Khafif and Maya Przybylski), along with assisting student Yuchen Zhang, curated Material Matters at the Design at Riverside Gallery. The exhibition showcased five design firms whose innovative projects combine material experimentation and digital fabrication. The exhibition ran from Monday, September 28th to Sunday, November 8th and displayed works by Emerging Objects (San Francisco, CA, USA), Matter Design (Boston, MA, USA), Radical Craft & G!LL!S (Los Angeles, CA, USA), Partisans (Toronto, ON) and Specific Objects (Brooklyn, NY, USA).
We met with Dr. Ila Berman on a Monday evening in her office to talk about the exhibition, the firms involved in it and the role of its theme in architecture today. The interview was conducted by Tin Huang and Chris Hardy and was moderated by Sneha Sumanth.
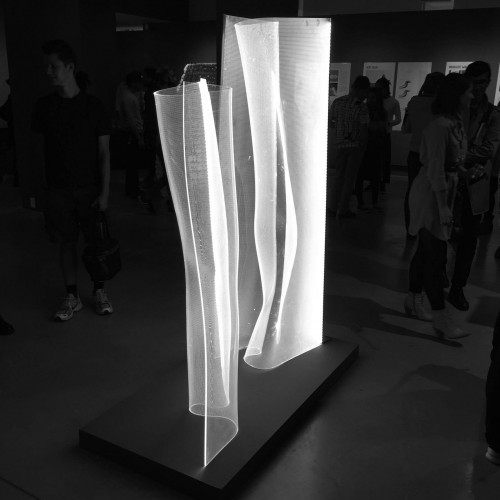
‘Gweilo’ by Partisans (photo by Tin Huang)
Chris: Could you speak to the theme and formation of the exhibition and who was involved, give us an introduction to it?
Ila: Sure, perhaps I could frame this within a slightly larger context. The exhibition was the first of a future series at the gallery on emerging practices. The idea initiated with the notion of emerging practices was that it might have a twofold direction: on the one hand to deal with the work of young practitioners, and on the other hand to focus on new types of practices emerging in architecture. It’s not necessarily a reference to the age or development of the practice but rather new and interesting things on the horizon happening within architecture, that would merit further exposure and discussion. This exhibition in particular was an attempt to refocus our understanding of digital practice. We are operating in a digital world and we often think of the digital as something that is immaterial, happening within the space of the computer or producing models for architecture. We don’t necessarily think of them as tools that actually produce architecture or architectural prototypes at actual scale and with real (rather than modeling) materials. So the idea was to foreground practices that are currently looking at the intersection between new technologies and design in different ways—using advanced manufacturing, robotics, 3d printing, rapid prototyping—while at the same time being focused on materiality and the ways in which it is influencing and being affected by these technologies.
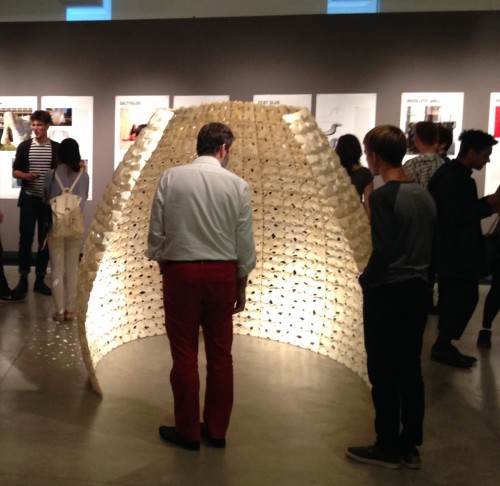
‘Saltygloo’ by Emerging Objects (photo by Nikola Miloradovic)
Tin: The exhibition focused on material innovation and digital fabrication. How does this combined method benefit architecture today?
Ila: I think there is currently a larger shift going on in the world of architecture in relation to technology. Architects are really trying to understand how technology can be used to change the way we make architecture or make components within architecture. At the same time some of the practices that are very focused on materiality are thinking about the idea of computation differently; through the notion of material computation. Material computation refers to the ways in which material might be self-organizing and thus “computing” its very formation. The example from the exhibition that exposes this the best is the Heap project by Rhett and Katrin Russo. This project is made of granular recycled ceramic and they developed a method to form surfaces by letting this granular ceramic flow through a series of templates. The templates themselves, which were perforated, were generated using a digital process. The templates have a series of holes in them, through which they pour these crushed ceramic granules. As they fall, there is a process of self organization; the material produces the formation. They are not pouring the ceramic into a mould; instead the material is forming itself. They are then studying the ways in which these formations are occurring,and then adjust or modify the parameters. Using different templates with different holes, they can then see that the material formations themselves transform in relation to the changing perforations and patterns. But what is really interesting about the process is that the heaps produce very precise formations and those results are fired to produce bowls or surfaces—the latter for a series of tiles that can be produced for architecture. This is an entirely different way of thinking about material, or the link between materiality and technology.
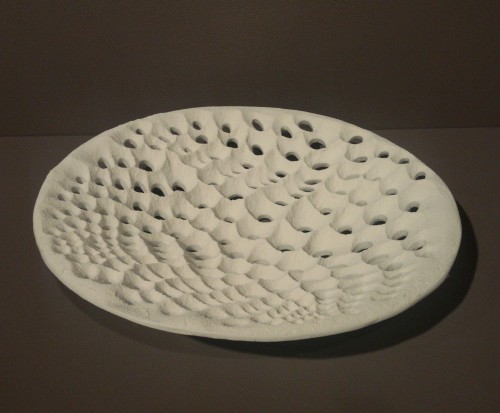
‘Heap’ by Specific Objects (photo by Kunaal Mohan)
Chris: Amongst the five firms, Partisans was unique in that it showcased its methods in designed and built spaces. What influence do you think digital fabrication will begin to have on our spatial experiences with architecture?
Ila: Using the Grotto Sauna by Partisans as an example—we could say that the fluid continuity of space that was produced is something that could have moulded by hand, and we might find these forms in more primitive architectures (with, of course, far less precision). But what we are seeing is that there is a strong relationship between the forms that we produce and the tools we are using to produce them. So one of the things that the digital transformed within architecture in the last fifteen to twenty years, was the fact that all of a sudden we had tools to develop continuous volumes and to morph and shift those volumes spatially. Something that was incredibly difficult to do if we were only using plans, sections and planar sheet goods. The evolution of digital tools enabled us to be able to mould material and to see the spaces that it could produce. But we were still stuck in situation where we must move between what we are capable of producing graphically, on the computer screen, and what we might be able to physically generate. Rapid prototyping tools, such as CNC mills and 3D printing, enabled us to then translate those fluid continuous models into physical space. Yet despite the fluid forms produced, these technologies still, however, operate based on a cartesian structure, which is really interesting, even though it is a microscopic cartesian structure that exceeds our capacity to perceive its striations. A 3D print is layering thin microscopic horizontal sections to produce something that is anti-orthogonal in nature—like a topographical model that you could be constructing for a site except with such small micro-scaled increments that you don’t actually see the incremental changes from one layer to the next and you don’t read these layers as separate forms.
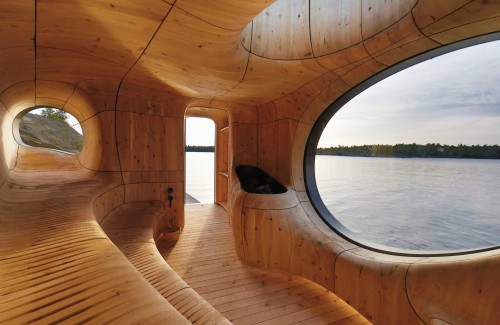
‘Grotto Sauna’ by Partisans (photo taken from Partisans’ website)
Ila: In projects such as the Grotto and Bar Raval the designers started with 3D printed models and then when working with a material like wood, had to understand how to translate those 3D print models into a physical artifact, because they could not use the process of layering microscopically thin sheets of material (even though that could be a strategy, and has been a strategy with other projects where a 3D sculpted surface has been made using striated layers of 2D laser cut corrugated cardboard). In their case they have been looking at other methods using CNC milling and the layering of thicker, material strata and through the use of robotics, where a 5 axis robot, can be used to cut a surface at any angle. With Bar Raval, one of the things they were experimenting with was the tool paths that result from the milling process. The tool path is something that most often designers try to get rid of since it is the unintentional residue of a fabrication process. In Bar Raval, however, they explored how the tool path moved across a surface and how it could become a design element—a physical part of the final product that helps to articulate the movement of the surfaces in the space. When you pay close attention to what went into making it, the workbecomes that much more beautiful and complex. The way in which each element gets cut becomes then pattern that is revealed on the surface of the material.
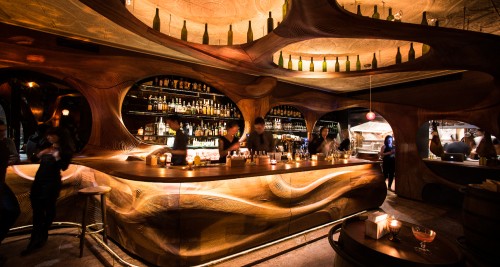
‘Bar Raval’ by Partisans (photo taken from Partisans’ website)
Tin: One of the centre pieces was Saltygloo by Emerging Objects, made of an innovative new material. How can a project like this extend beyond the scale of an installation? What are the implications for a larger architectural discourse?
Ila: I think that as an experimental practice Emerging Objects is extremely interested in the development of full-scale prototypes. Even though Saltygloo is still operating as an installation, for them it is a full-scale prototype. They are looking at how you might make a component using 3D printing with materials that will be durable, and potentially withstand weather (for exterior applications) and that these materials can be used to produce the final architecture. Two of theother pieces in the exhibition—Bloom and the Seat Slug project—are far more durable and meant for the outdoors. They couldn’t be brought into this exhibition, however, because of their scale and weight. Its certainly far more difficult to move full-scale architectural projects! What is interesting about them is that they are 3D printed with sand and/or concrete mixtures used to make final building components. They expend a lot of energy in their practice investigating the relationship between the component and the formation of that component. I don’t know if you noticed, but within many of their projects, the logic of the actual component—its boundary conditions, for example—is not evident when you look at the piece. The seat slug appears to be highly fluid and continuous across the surface—a pattern that actually conceals the seams of the piece (and the fact that it is made up of discrete units). The difference between the ways in which they continuously pattern the surface and the individuation of blocks or components is part of their design research. I think that they are a very important firm in relation to the next phase of digital fabrication because they are asking the question: ‘How do we make architectures using these rapid prototyping techniques?’ and ‘How do we generate different kinds of materials that expand the capabilities of the technologies to produce real material architectural artifacts?’
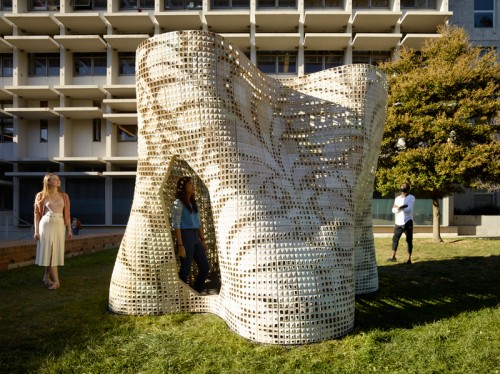
‘Bloom’ by Emerging Objects (photo taken from Emerging Objects’ website)
Chris: Would you say that 3D printing,with materials such as concrete and sand, can essentially replace masons or bricklayers?
Ila: Well, 3D printing is applicable to the development of the individual components—the bricks, blocks, or building units in whatever form. There is still the necessity to assemble them. The bricklayer isn’t necessarily the one making the bricks. The bricklayer is actually assembling the structure. So when we are dealing with individuated components as part of a structure, you are always going to have someone (or in the case of robotics, a robot) assembling the components. The difference might be in the ways in which they get assembled. When there are unique components as in the case of Saltygloo, each single component occupies a unique position in relation to the larger whole whereby its location (in the case of Saltygloo) is indexed on the piece. This is often marked as part of the fabrication technique. In Saltygloo for example, each piece was marked by a letter designating its row or vertical location as well as a number indicating its horizontal location in the row. The process of assembly is still an important part of the construction. It means perhaps that the rules for assembly are critical to the making of the work since mass-customized elements also might imply nonstandard forms of assembly as distinct from the use of a readymade industrial element that can be placed anywhere in the system.
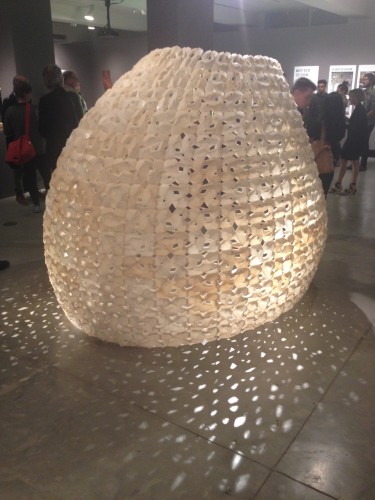
‘Saltygloo’ by Emerging Objects (photo by Hagop Terzian)
Chris: The works of Matter Design are interesting in their reference to the vernacular, with innovations in scale and typology. They transform the idea of the module, where each piece is uniquely fabricated. What are the practical applications of unique fabricated modules compared to traditional standardized blocks?
Ila: We could take an example: the Round Room. The vernacular artifacts they were referring to in this project are the Inca stone walls. We don’t fully understand how they managed to build Inca walls with such precise formations, each block was unique, and cut by hand. Yet despite the high degree of differentiation of the stones, their shapes, they always fit perfectly together without the necessity for mortar. In Round Room, Matter Design construct a contemporary version of the Inca stone wall where each block is unique in its form occupying a very specific position in the overall formation. They are then perfectly fitted together. Because this piece is based on a digital model it conflates the idea of division (the division or tessellation of the surface) with addition or aggregation. They are unique additive elements that aggregate to produce a continuously sculpted surface, each a perfect fit. The work is both unique at the scale of the element and at the scale of the whole. And of course every stone has to be a different shape and size because of how it is positioned within the overall form—the space is not composed of flat surfaces or orthogonal walls. The Round Room was primarily conceived as an interior space. You would slide into the space through a small opening. From the inside it was this beautiful volume.
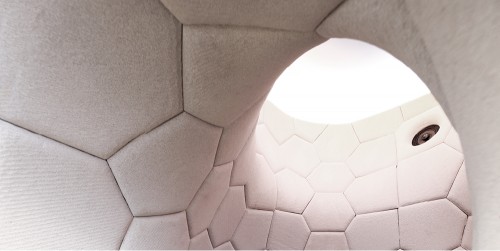
‘Round Room’ by Matter Design (photo taken from Matter Design’s website)
Ila: A second piece by Matter Design—La Voûte—rethinks the vault which is now constructed out of wood. The vaults are made up of hexagonal forms that are not only differently shaped and sized, but also had varying degrees of permeability based on the size of their circular perforations. At the very top, for example,there were larger perforations to lighten the surface and perhaps to let in light. As you move down toward the ground, the perforations shrink and the surface transforms into the columns that support the work. And the columns weren’t made up of an aggregation of components. They were made of a single element,yet the aggregation is still marked on the surface of the columns to render them continuous with the vaults. This couldn’t have been created or built in the same way using either traditional manufacturing or design methods. Matter Design is perhaps trying to rethink a historical archetype—that would have taken manyyears to build—through a new material, form and technology.
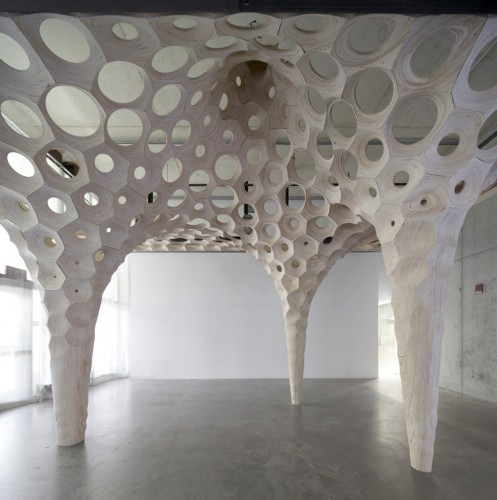
‘La Voûte de LeFevre’ by Matter Design (photo taken from Matter Design’s website)
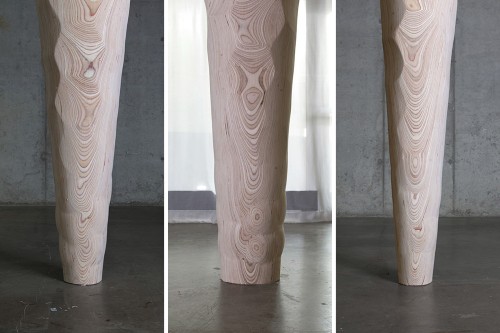
Detail of the columns in ‘La Voûte de LeFevre’ (photo taken from Matter Design’s website)
Tin: Specific Objects’ material innovations begin to reveal form and use through methods of casting. Do you think works like this can feed the mass production and consumerist mentality of designed products today, or are these experiments purely research oriented?
Ila: One of the notions of mass customization is that the uniqueness of ourselves might have particular ramifications in relation to the objects we produce. If we think of it in relation to clothing, it’s the idea that perhaps I could now go into a store and instead of finding a style or size of jeans that fit me well, I could have a pair fabricated instantly that would be made to fit me perfectly. I walk into a dressing room and there is a technology that scans my body and can now produce for me a particular pair of jeans made for my body. I’m not a tall person, and every time I sit in the classic ergonomically-designed chair made for a range of body types, inevitably my legs will be swinging in the breeze…so the notion of mass customization could be that I can get one of those ceramic stools designed at a slightly different scale by shifting a parameter (or range of parameters). Because there is a formula in production, we can think of the parameters as being controlled by an algorithm or rule set. If we change one of the variables we change a specific iteration of the design. So instead of designing singular objects we are designing a series or a ‘family’ of artifacts with shifting parameters. From the consumers perspective, it gives you more choice in relation to the specificity of the work, and that specificity could be in relation to the particulars of my environment, body type, etc. If we want to purchase a car and customize it with certain features, these are selected from a given set of elements that have already been designed and made based on research of what consumers are interested in.Parametric customization, however, is pushing one level beyond that, such that a product can be made for you; not an entirely new design, but developed according to a set of parameters to fit whoever the consumer might be.
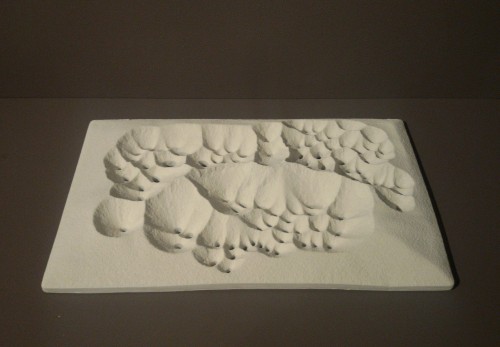
‘Heap’ by Specific Objects (photo by Kunaal Mohan)
Chris: There is an evident return to the importance of the artisan today, perhaps to address a sense of physical detachment we feel with our built environment. How do you think material experimentation can relate us to long standing ideas of craft, making and empathy?
Ila: I think that part of the reason that these works are important is that they promote an idea of digital craft with the understanding that digital technologies give us new tools, just like any other tool, yet with new capacities. In making, however, we are still going to be dealing with material. And of course, the notion of the title—Material Matters—is a play on the hybrid meaning of the two words. It’s saying that the role of material is important and at the same time that we are dealing with different types of matter and logics in dealing with materials. So it’s about the relationship between the logic of the material and the logic of the technology. When I was talking before about the Heap tiles, there is a specific material logic that is intrinsic to the work. If a different kind of material was used, it wouldn’t form (or ‘materially compute’) in the same way. The microscopic properties of each granule in the ceramic in relation to the perforated template patterns and the act of sifting is what determines the form. What is critical here is the relationship between a particular material and a particular technology. I think this is really important for architects. I’m saying this because as architects, we are essentially form makers. We are not the ones out there building the works we design. And often that gives us a detachment from materiality. Very few studio projects start with the exploration of a material. There is the idea that you are making a form and that you can fill it with any material—this is referred to historically as the hylomorphic model, the idea that matter has no logic of its own and can be used to fill out any form. The opposite idea is that materials have their own internal logics. Wood has a grain. I can bend it. If I cut or follow the grain, I discover an incredible elasticity specific to the internal formation and structure of the wood itself. If I cut across the grain I will discover very different properties. So being able to experiment and discover the relationship between materials and technologies is important for architects. Essentially, such forms of investigation will make you a better architect because it will enable you to understand that material is not just about visual surface effects—an imagistic reading of materiality that is supported by the ways in which we use material palettes in rendering surfaces. Materials have actual properties and qualities that go far beyond the surface.
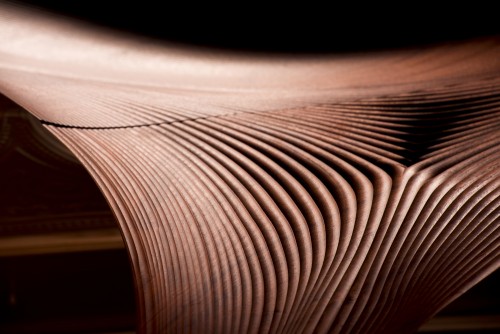
A detail of CNC work in Bar Raval (photo taken from Partisans’ website)
Sneha: Thats interesting because I have been thinking about how materials have certain inert laws that we follow. And when we used to use them according to vernacular methods, the material was the law and form would follow that. We couldn’t really manipulate that but perhaps today we can. With the same materials today – wood, concrete – we can manipulate them a bit more. And the relationship between the architect and the material is changing, we are gaining more control.
Chris: With the capabilities of digital fabrication producing unique and new building prototypes, what do you think the role of the contractor and the builder is today? Is the designer beginning to take on these roles?
Ila: I think it’s really important that the designer takes on these roles in some capacity. Over the years architects have given up a lot of control (and responsibility for the making of buildings), to the extent that they’ve lost control over the production of the final work since contractors essentially have control over the means and methods of construction. One of the interesting things about digital technologies is that they have enabled architects to not be limited by the skill base of those that are making the works. And I think that is a critically important part of the process. We can say that it’s enabling a new freedom and a new level of control for architects. There are some architects operating within small experimental practices that might take on design build as their trajectory, and in this process they might enable the generation of artifacts that would otherwise never get built. And often those practices, as they get larger, lose the experimental qualities of the earlier works because they were built in a particular way. Technology as a communication device is changing this by replacing a set of drawings that need to be decoded and interpreted by someone to become instructions for making, with a 3D model that can be directly linked to a fabrication technology ensuring that the final artifact produced is true to the design. But that also means that the architect has the responsibility to understand precisely how that artifact is to be made. So having all that control means needing to have more knowledge and experience and take more responsibility in relation to fabrication, but ultimately I think that we will end up with better works of architecture if we take this on.
Sneha: So in terms of the communication of design that we now have, how do you think that clients will begin to respond to this? Instead of viewing the standard drawings we communicate with, they will now be interacting with technologically advanced ways of communicating design. How will the relationship between architects and clients change because of this?
Ila: Traditionally clients were looking at plans and sections (which they still refer to as blueprints even though we haven’t been using this technology for printing for many years) although, for the most part, most lay people aren’t able to read plans and sections well to begin with, The new digital tools that we are working with enable better communication—like three dimensional visualization—renderings that are much easier to communicate to clients, like walkthroughs where someone can see a 3d model, zoom in, move from one space to the next. So it has enabled us to communicate far more effectively. As an aside, one of my thesis students is dealing with virtual reality as a tool of communication so that I can put on a headset and move through the virtual space of a project that I might be designing and experience what it might be like. These tools are certainly different from those tools that we have been talking about but are part of the expansion of design technologies that we should adopt as architects that make the design and making process more interesting and effective.
Feature Image by Tristan Van Leur
To learn more about the exhibition visit DATALab’s website.
Sneha Sumanth is a graduate student at the University of Waterloo School of Architecture. Her role in BRIDGE involves overseeing the website and publications. Her thesis work looks at the relationship of energy and architecture in the offshore infrastructure of the Santa Barbara Channel in California.
Leave a Reply