By: Melody Chen & Riling Chen
At the Waterloo School of Architecture, the art of making is integral. Model-making and fabrication are a component of every studio course, often with a required final model. For some students, their interest has veered further towards the craft component of architecture. We wanted to interview these students to ask them—how can craft influence the design process? In the last part of this series we interviewed another one of our undergraduate students, Tomoki.
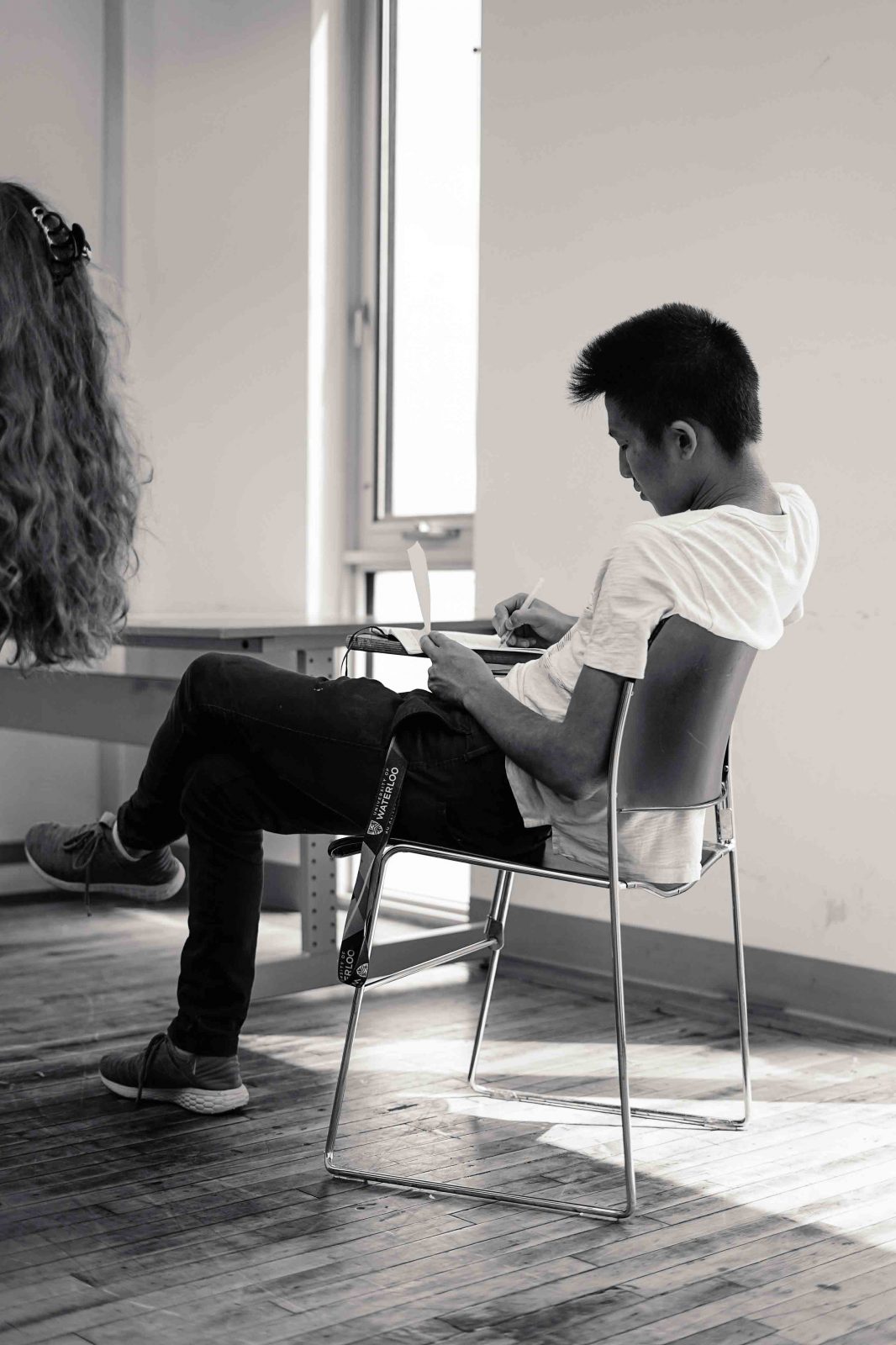
What drew you to work at a fabrication studio versus an architecture one?
I’ve always liked making things. So I started with fabrication and then went into architecture.
Then why pursue a study in architecture?
Fabrication led me to architecture because it was a way of designing that went beyond just making things for yourself. It questions things like how are you going to help your community or how can the things you make impact people?
What projects did you work on at the office?
I made a sculpture that a developer wanted and I got to do metalworking for the first time.
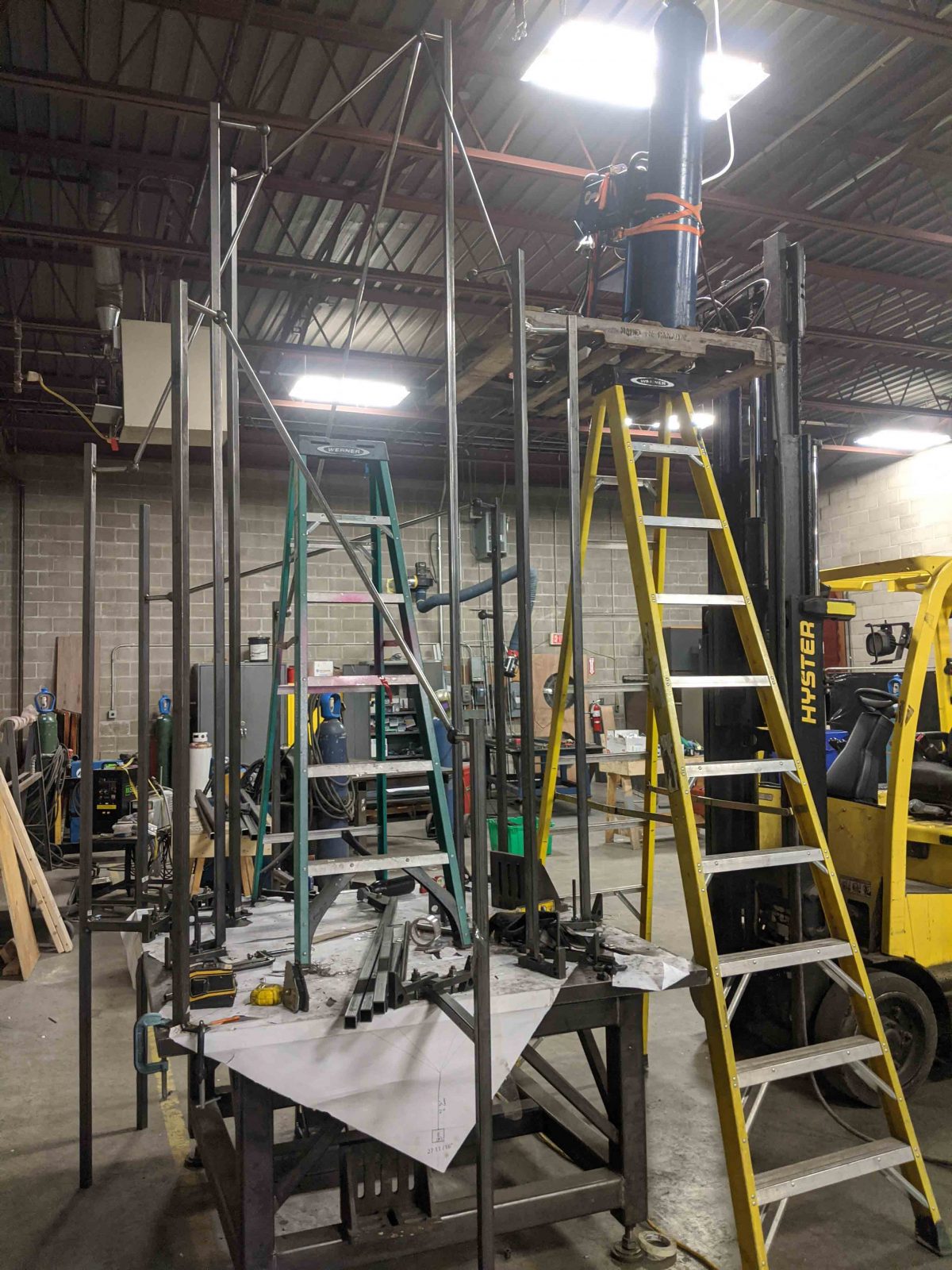
How was the experience learning a new skill?
It’s pretty fun. My boss is a fun guy, so he makes the process very fun. He teaches it in a very philosophical way. When he taught me welding, he told me about the state of mind you have to be in is more important than the buttons you have to press and the movements you have to perform.
What is the state of mind?
He explained it as a very intense process because once you do it, it’s done. So you have to prepare your whole body and make sure to be comfortable. The sound has to be right, the right amount of heat has to be applied, and you have to move your body with the right speed. When you mess up a weld, it can look really ugly. You don’t always grind it, so you want a nice weld. But I’ve had a lot of bad welds.
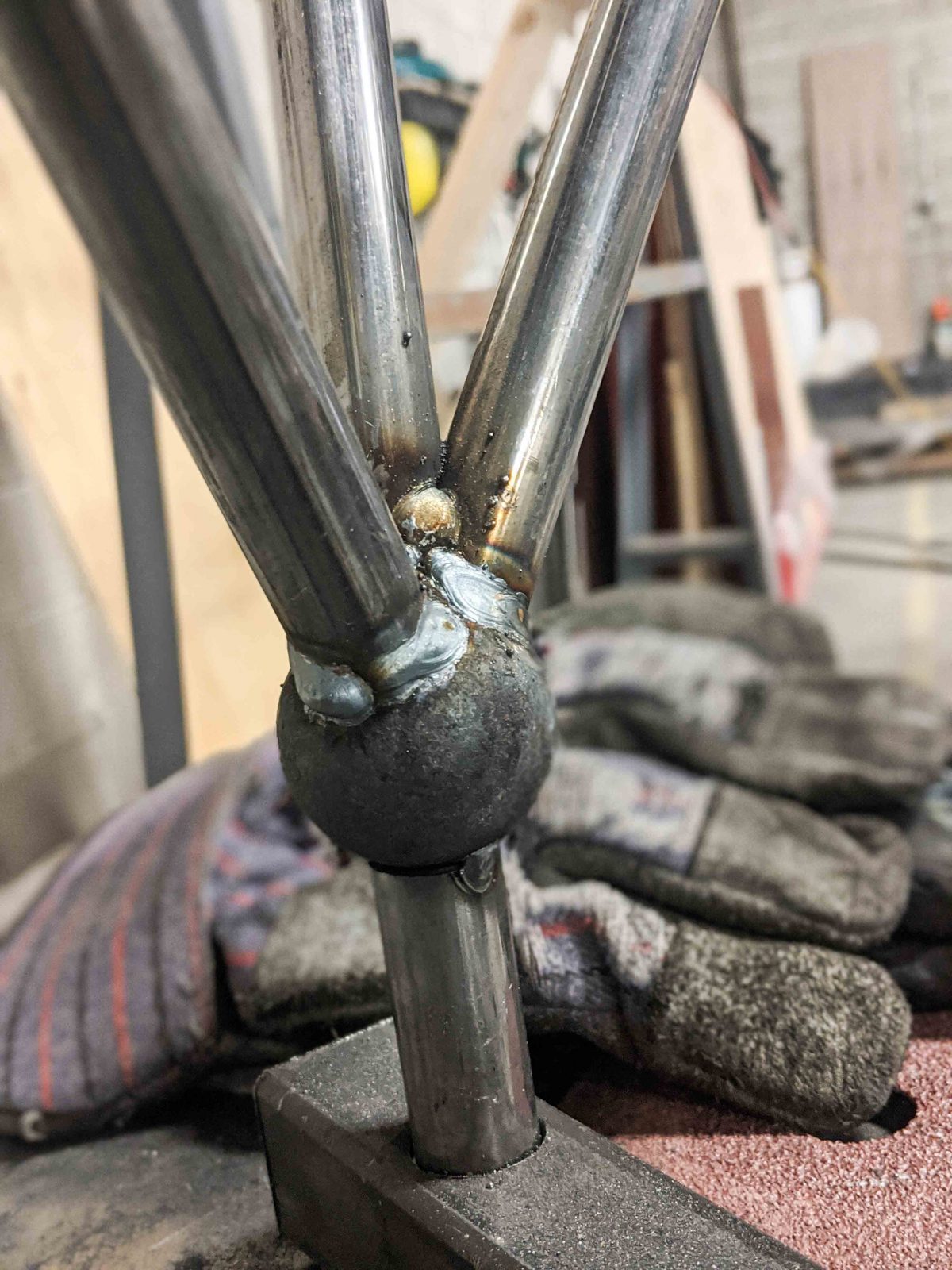
Fabrication is pretty interesting because everyone has their own way of making, there’s no “right” way. If I want to figure out how to make something, I can ask five different people in the shop and I’d probably get five different answers on what’s the best way to make it. Because of that, it makes every fabricator or metalworker unique.
Is the sculpture currently in development?
It was supposed to be done but it’s on pause right now. I’m not really sure what’s going to happen with it.
What was your first encounter with fabrication?
There was a kid in my kindergarten class who happened to have the exact same hot wheels backpack and lunch bag as me so we became friends. I found out he also liked making things so we taught each other how to put together motors and we made our own paint spinner. It’s a weird thing where you attach a piece of paper to a motor and then you drip paint on it to make a swirly effect. The fun part was figuring out how to put together the motor. It came in a kit with the batteries, switches, lightbulbs and everything.
How did you figure out how to make it?
During library class as a kid, we were supposed to take out a different book every week. But we just took turns borrowing the same electronics build book. Between the two of us, we pretty much had the book for the whole year. It was the only thing we read.
What’s the difference in thinking about fabrication design versus architectural design?
It’s the equivalent of the contractor to the architect. The fabricator is the contractor of artists and sculptors. We’re at the end of delivery for projects.
So you get commissions from artists to make sculptures?
Yeah, the artist draws something that they want made and we make it for them. Only clay sculptures or artists really make their own things. Most of the time street art is made by a fabricator. To me, the biggest difference between an architecture studio and a fabrication studio is the size of the team. The guy who draws all the details is probably sitting right beside you and so is the guy who installs it on site. And the thinking is a lot in the “how”. The construction drawings that an architect gives us feel like a schematic diagram. We take the CD’s and we have to give it very specific products, decide what kind of bolts we are going to use and what order it’s going to be assembled in. It’s a lot of problem-solving, improvising, and experimenting on site. Because oftentimes you make a sculpture for a room that you’ve only been to once and you’re expected to install it on site in a day. You have to think about how to get it there without damage.
Do you make a lot of mistakes since a lot of the problem-solving is by experimentation?
Yes, inherently fabrication works within a realm of imperfections and tolerances. If somebody asks for a square planter, it’ll never be a true square. So you have to think about how to minimize the distortion from welding and how to ensure the reveals are hidden. How are you going to make it in a way where there’s the least amount of opportunities for mistakes? At our shop, we do POM drawings. POM stands for “point of mistake”. When we’re making something we always build off a drawing, so we try to mark out points where it’s okay to make a mistake or places where we have made mistakes in previous versions.
So it’s rare to restart a project when a mistake is made? You’re always finding a way to work with it so that you can move forward but minimize the amount it’ll actually affect the product?
Exactly
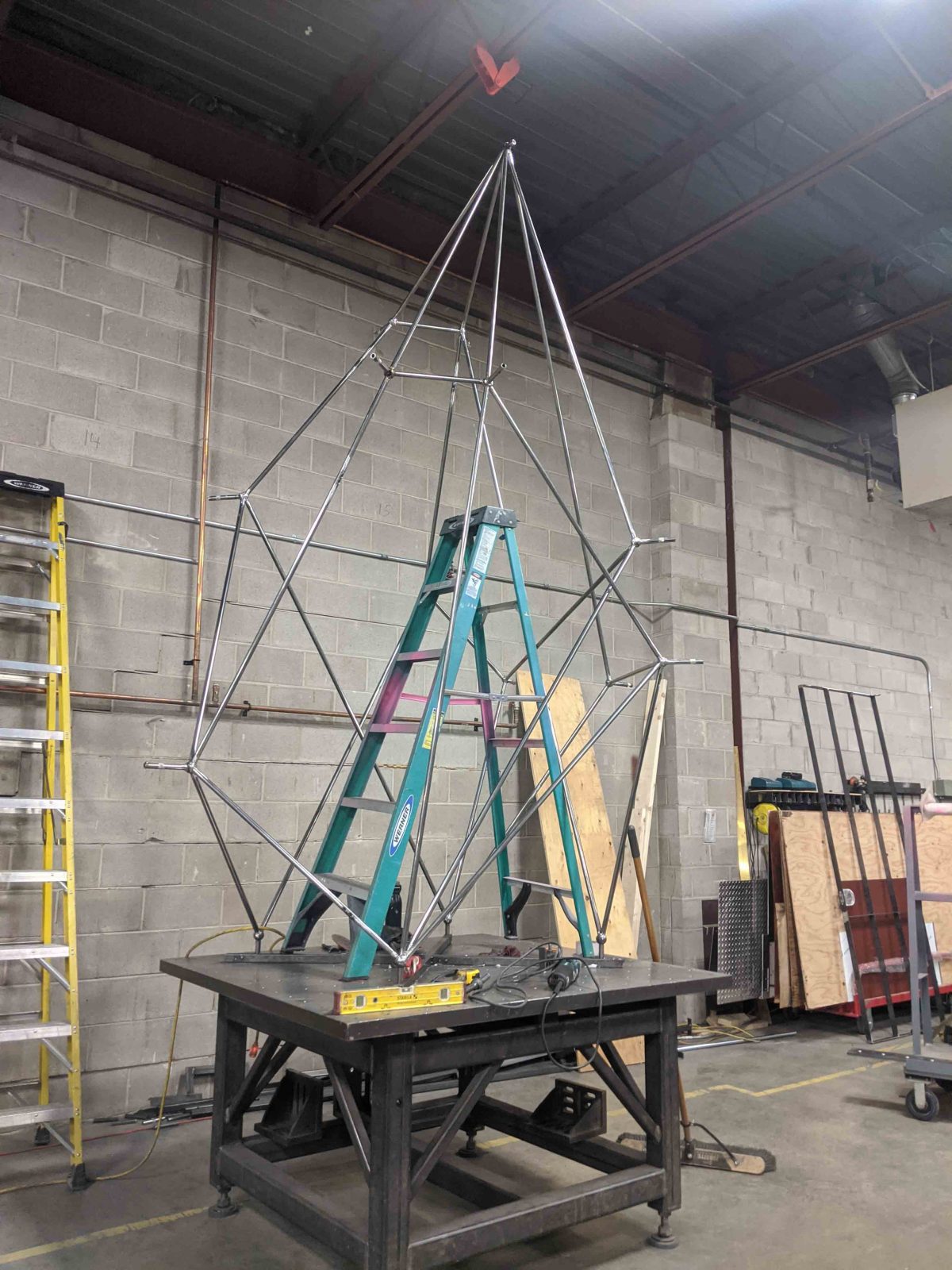
This was the handmade part of the sculpture. The outer part is 3D printed and calculated for on Grasshopper. This part is the inner structure so it has to be stronger. It’s made of steel that’s welded. The outside is 3D printed with aluminum and it’s more artistic and sculptural. This part has to fit through a normal door, so there’s a lot of hidden connection points. The idea is that the whole thing can come apart and split into two.
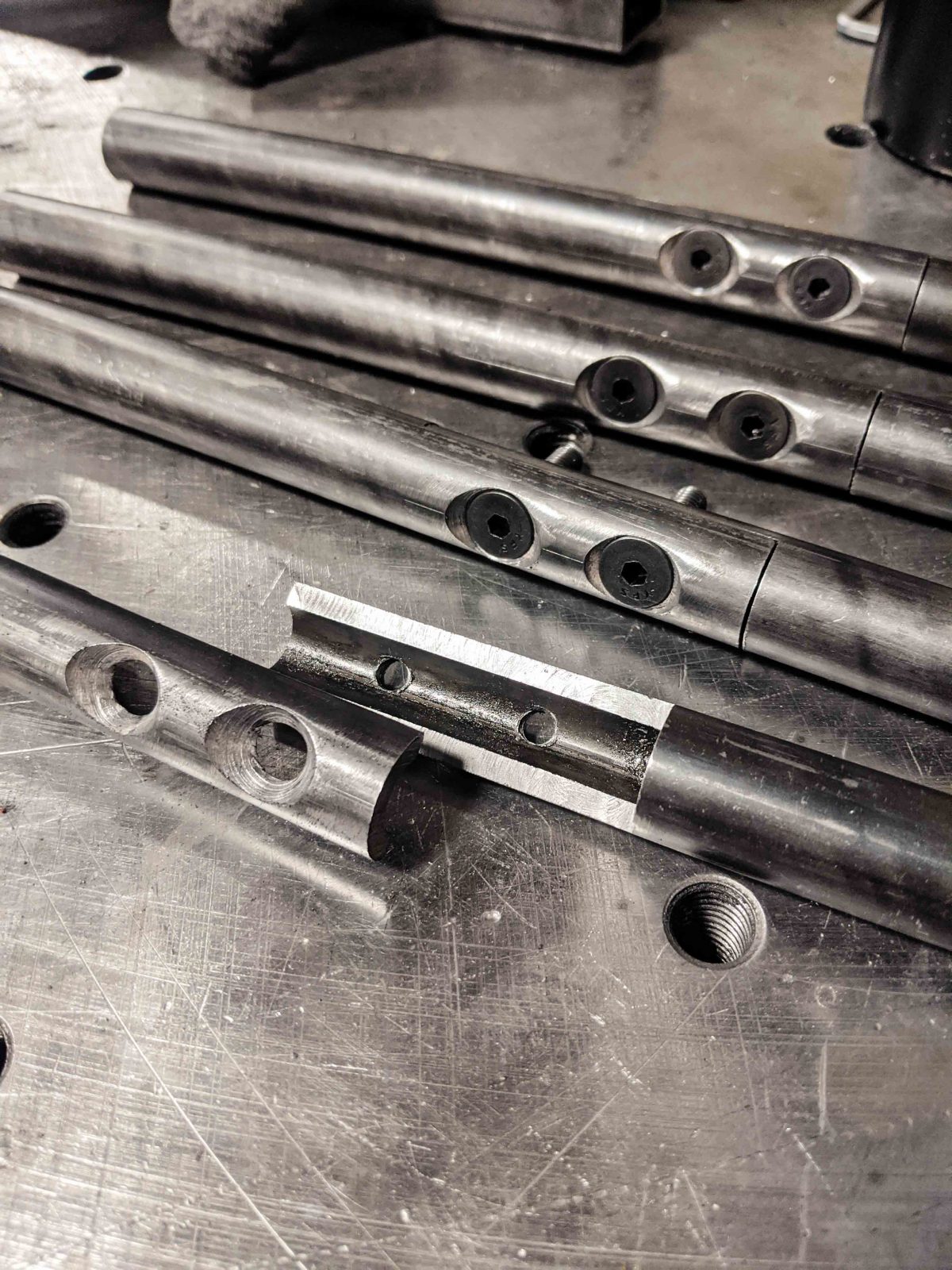
This was something that we didn’t account for in the beginning. It used to be a whole piece, For a few weeks, I spent a lot of time cutting it in six different places to insert those joints.
You start with a round tube and then I cut it in an L shape. So in order for the two flat surfaces to meet, it had to be machine flat. It’s a lap joint that’s machined.
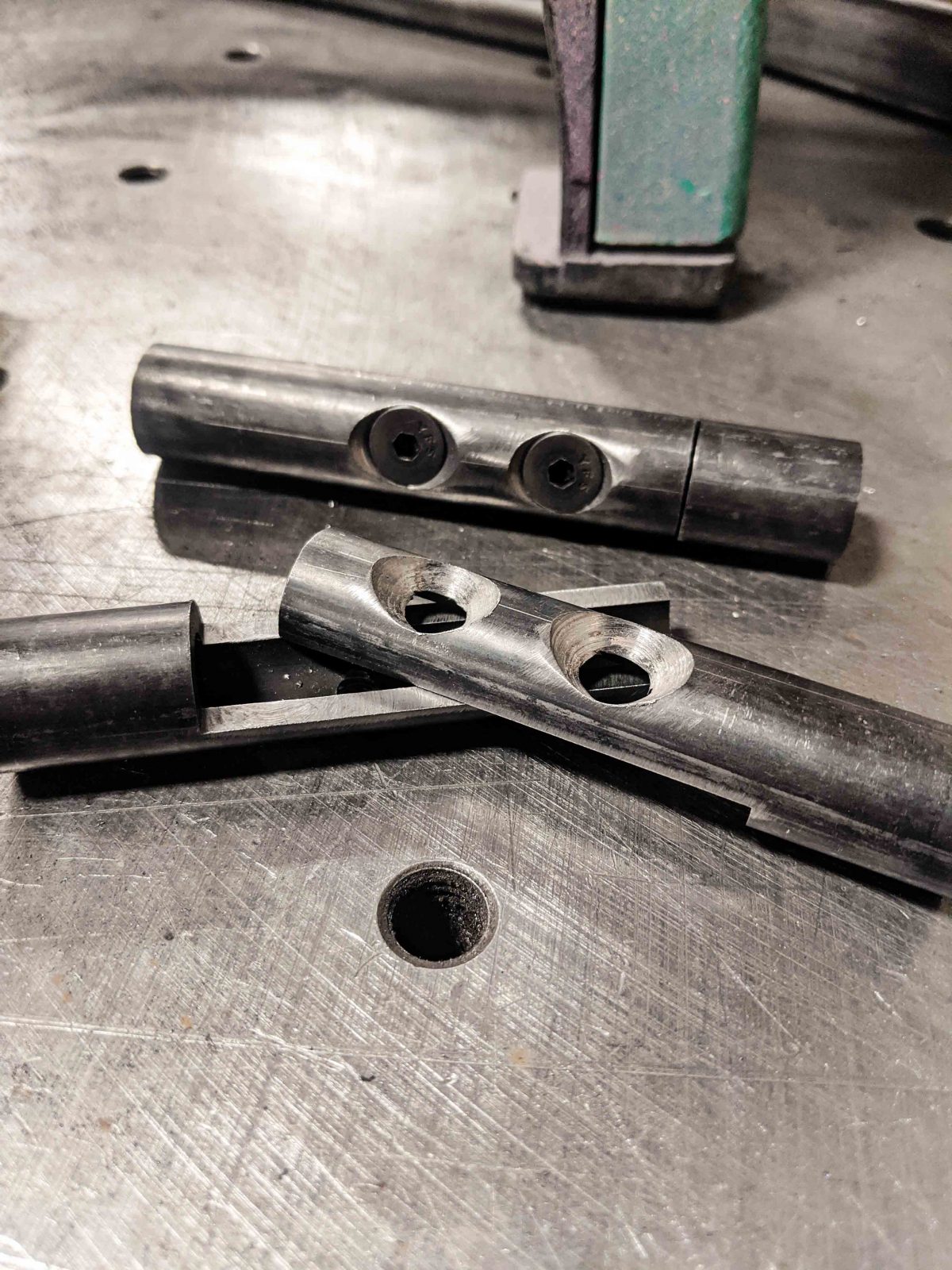
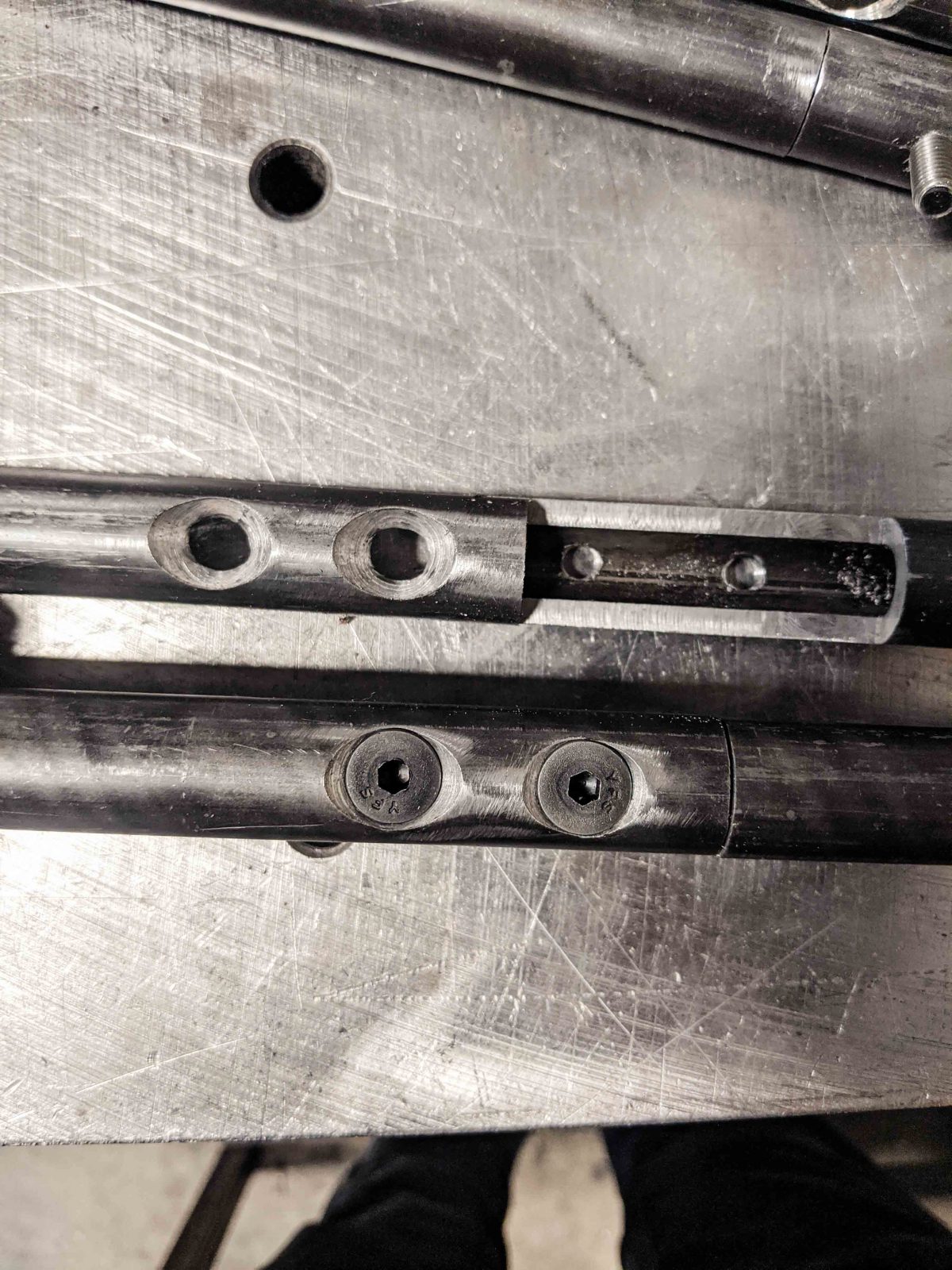
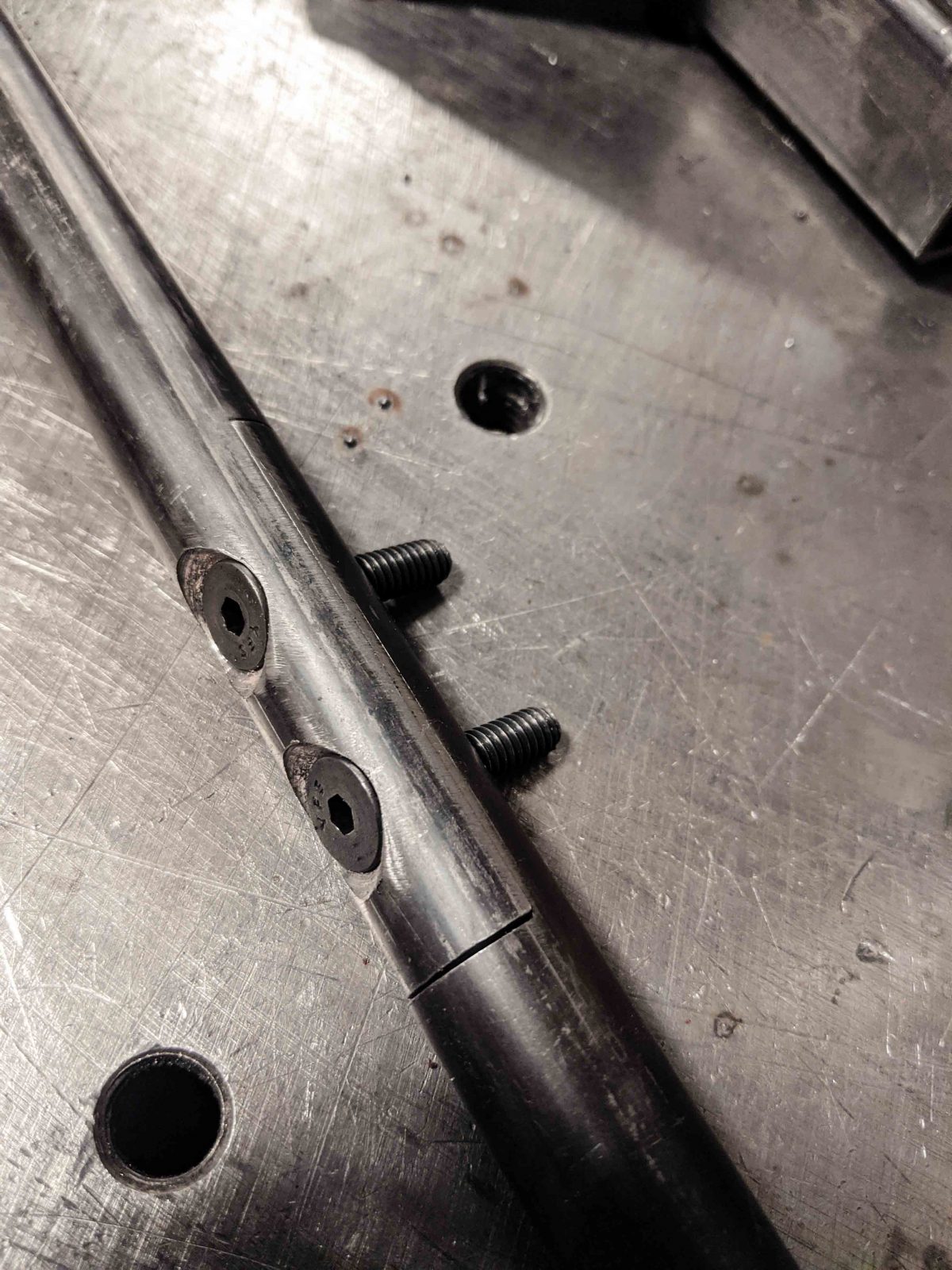
If you ever make a bad weld, it’ll be high up so you won’t really see it and it’s going to be powder coated. Powder coating is similar to how they paint cars. They statically charge the metal and you get little bits that colour the metal. It’s sort of like spray painting. By charging it, you can control where the paint goes.
Here’s how it looks grinded and polished. When it gets powder coated everything will have a consistent look to it.
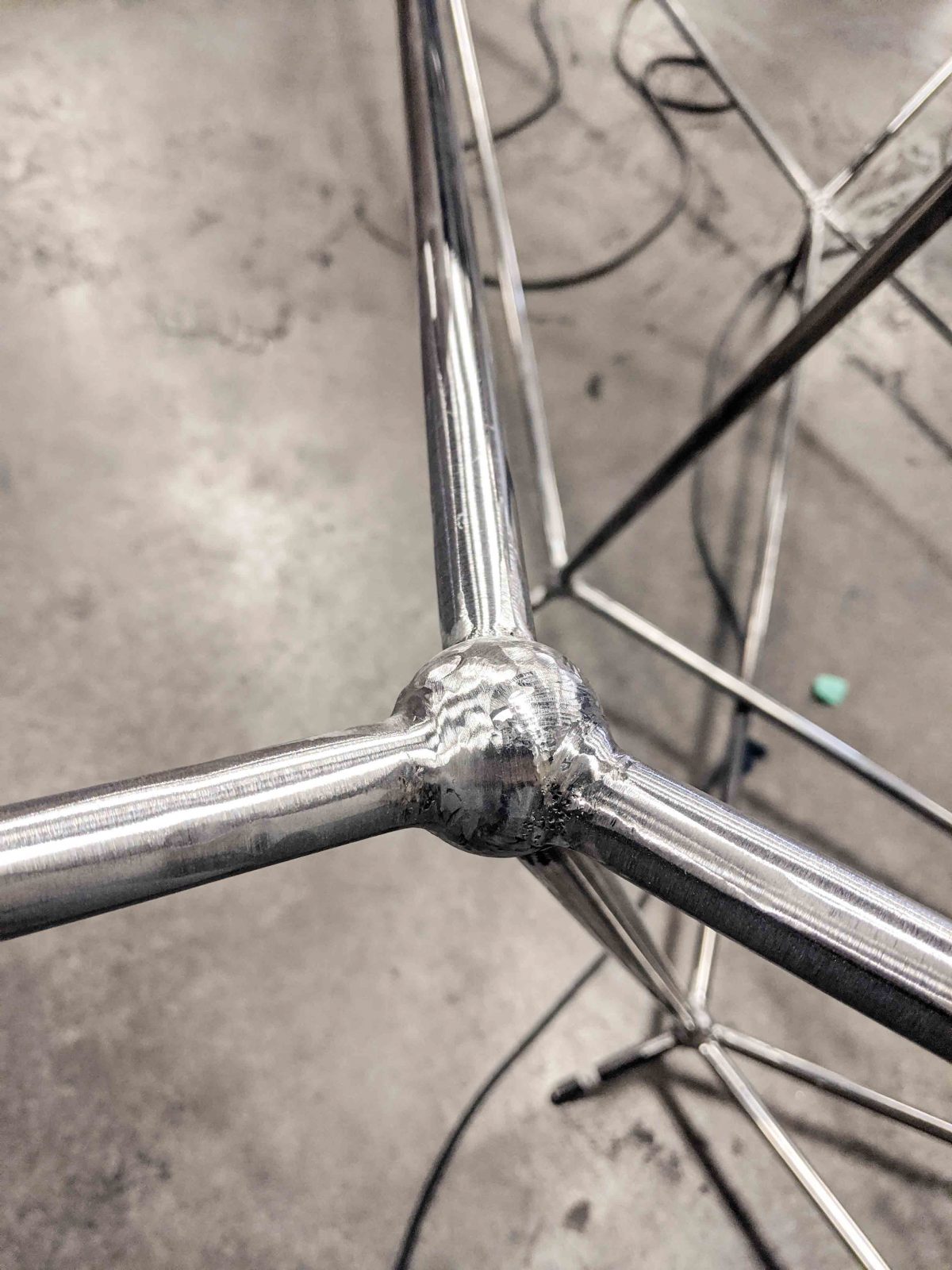
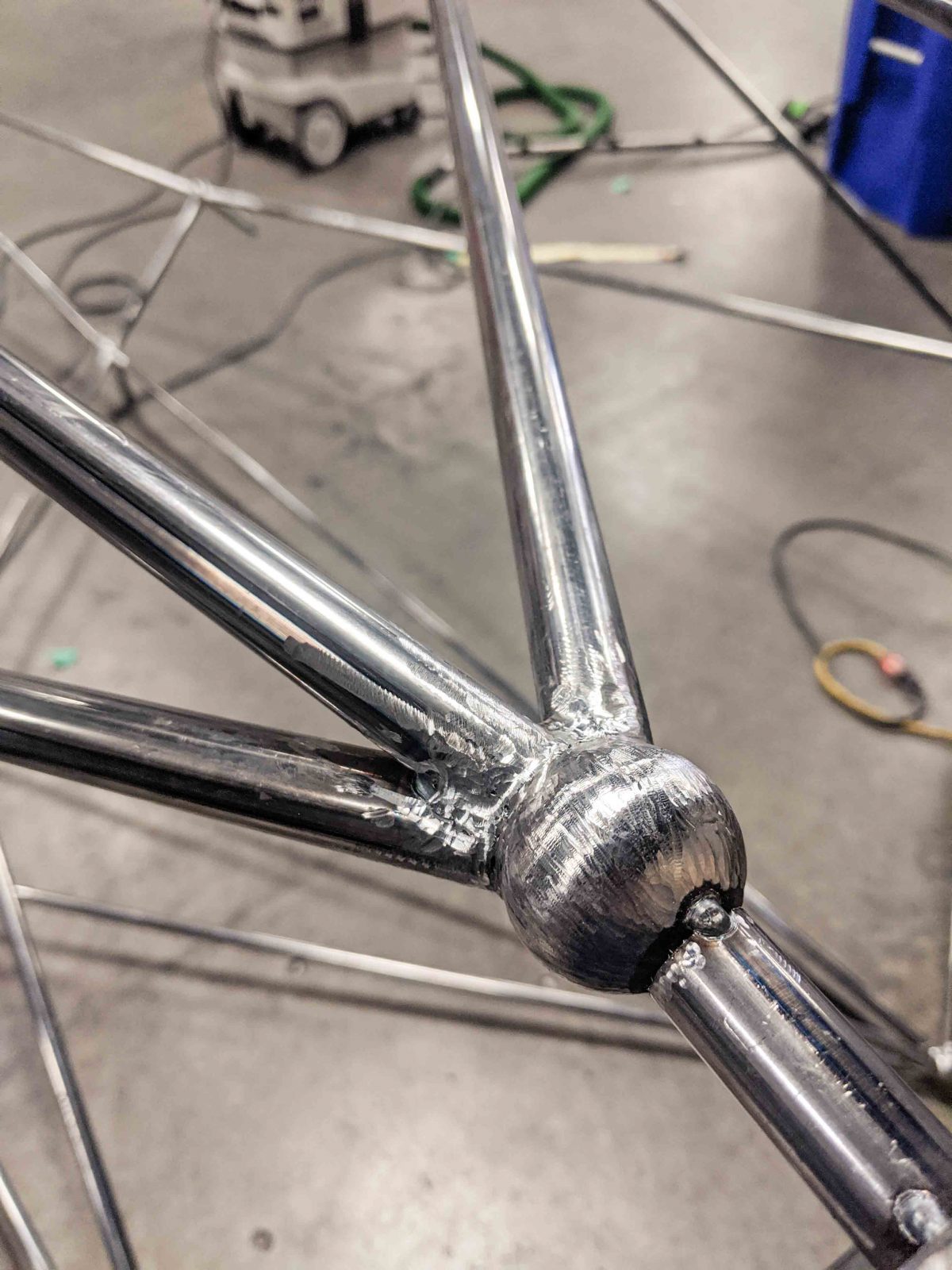
What would you say is your favourite medium to work with?
In the shop, I’ve only really worked with metal. I did a little bit of woodworking in Grade 10. I’m not sure which one I like better yet. They’re very different but also similar. Metalworking is like woodworking with bigger tools. It’s all the same tools but amplified. It’s stronger, louder, and more intimidating. But it’s the same in the sense where you start with a piece of lumber. In metalworking you also have your same stock, like you can choose between a flat bar or a tube.
Do most fabricators specialize in one medium?
From what I understand the word fabrication is for metal. It applies to metalworkers. But everybody specializes in different things. Most people who come to us know what we do, so they come to us for that reason. The two studios that I worked for were more on the artistic end. There are a lot of industrial fabricators who are only interested in making structural staircases or basic railings. For us, we work more with artists and designers who want public street art. The guys I worked with are OCAD grads, so they’re more interested in making art.
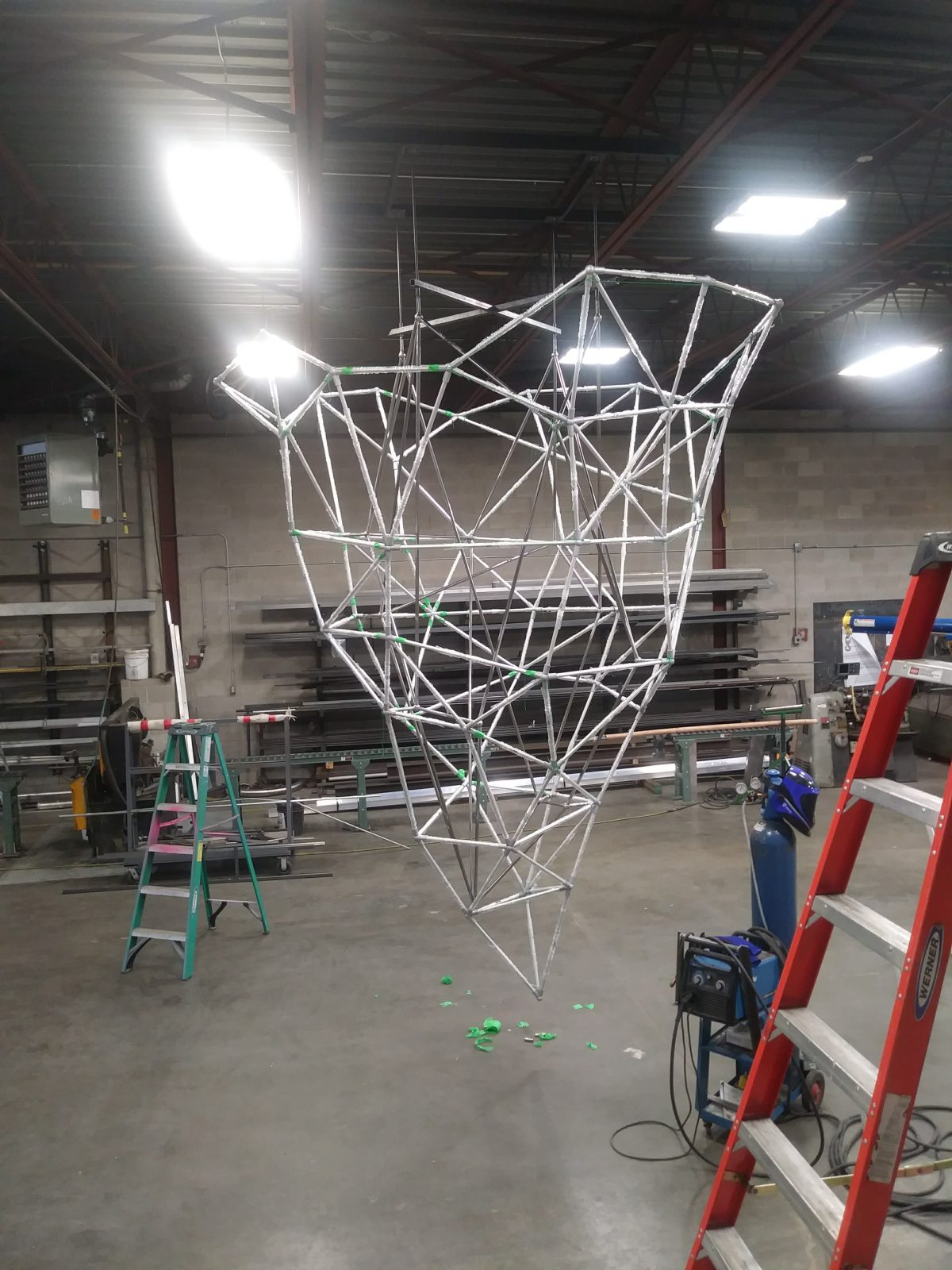
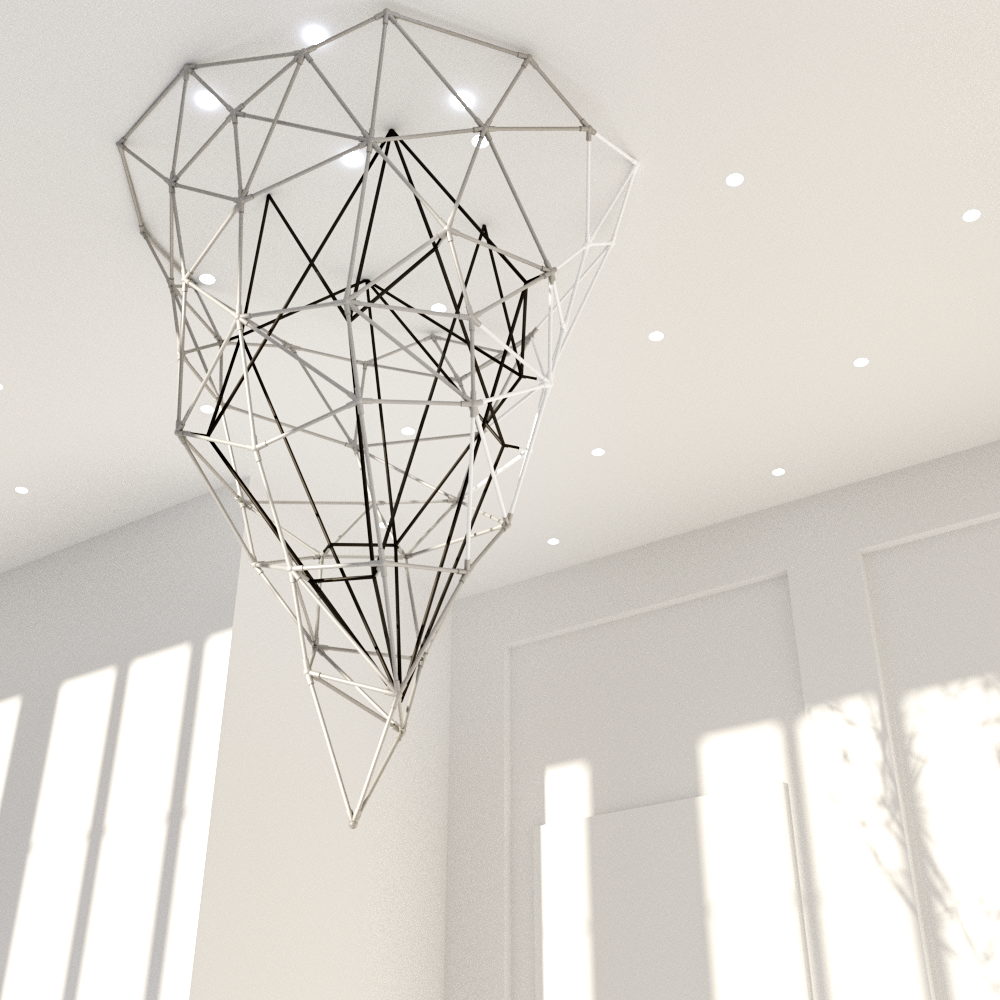
Leave a Reply