By: Melody Chen & Riling Chen
When the Bauhaus opened in 1919, it was a stark shift from the traditional form of teaching the arts. They believed that artists should return to craft and instead of the typical teacher and pupil dynamic, the school was filled with masters, journeymen and apprentices. Their philosophy was simple, students should be able to live in and build the forms that symbolize their environment. At the core of the Bauhaus, this way of teaching would free the machine from its lack of creative spirit.
At the Waterloo School of Architecture, the art of making is integral. Model-making and fabrication is a component of every studio course, often with a required final model. There are also supplementary courses such as digital fabrication (taught in 2A), woodworking, the chair course, and several optional studios held in the 3B term. For some students, their interest has veered further towards the craft aspect of architecture. We wanted to interview these students to ask—how can craft influence the design process? The first student we interviewed was one of our master students, Nathanael.
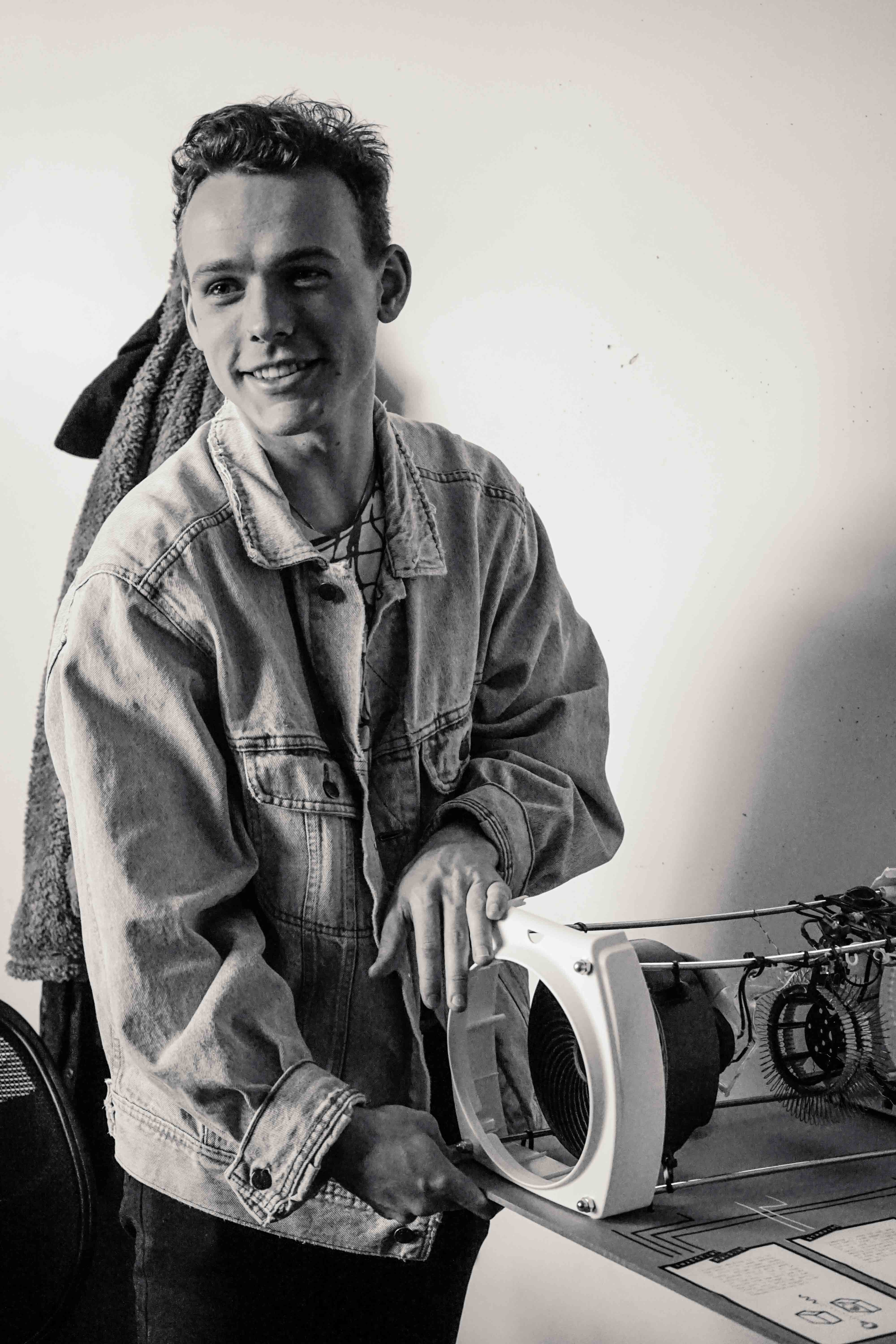
What is your thesis about? We see you drilling stuff on Instagram all the time.
I am exploring how people interact with designed objects and the current issues surrounding repair and product lifespan. An example is product obsolescence. I’m investigating the other side of that and how designers can create products that account for people who want to repair things and extend the lifespan of their products. It’s like designing for a do-it-yourself approach.
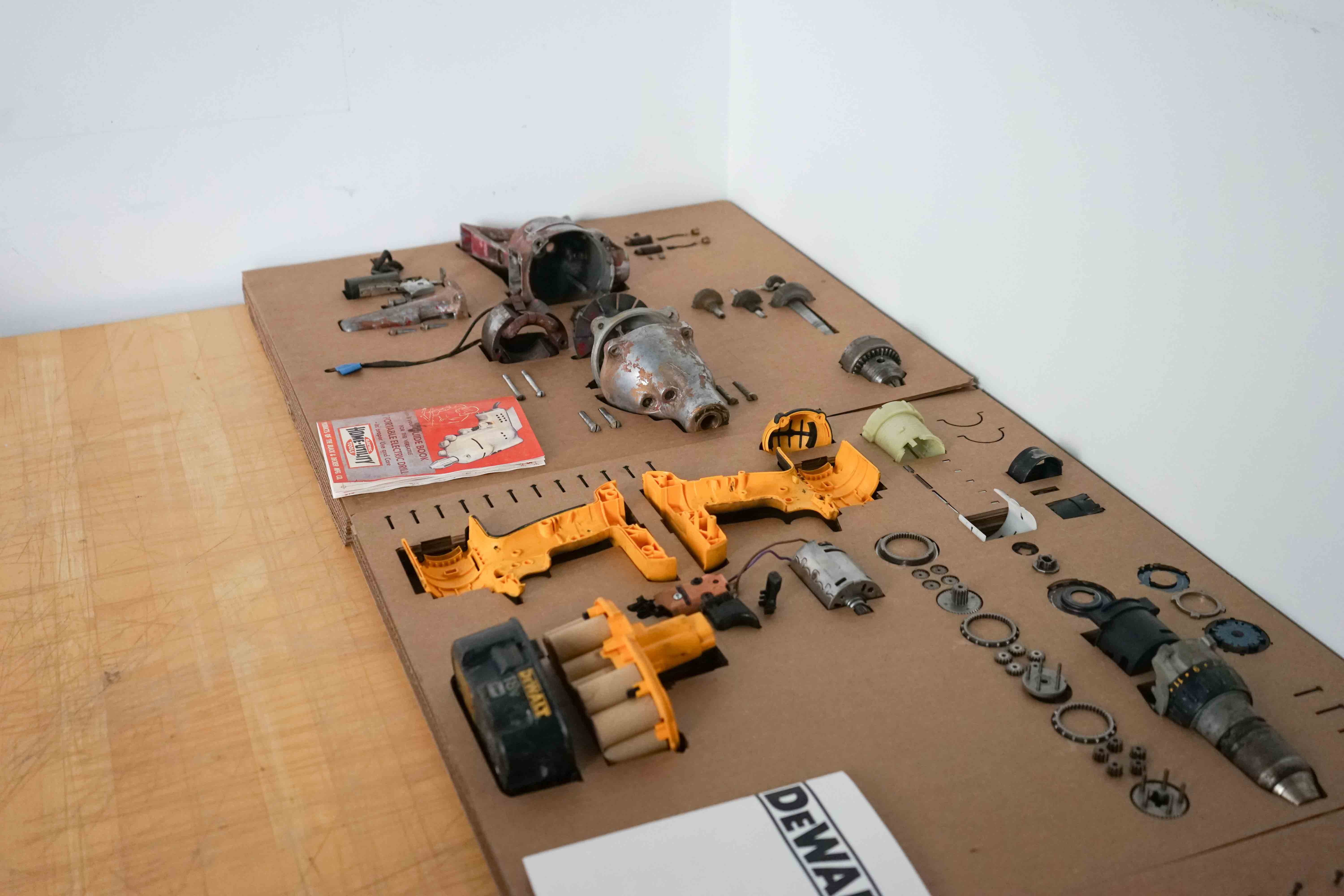
Building off of that, what’s your opinion on mass production?
I think it started as a great thing because it made things available for everyone. But one of its big problems is the cheapness of how things are made. Some products are even worse because they’re designed with planned obsolescence, which means that they’re planned to break so that you have to buy a new one. There’s also selling into styles, where you have to buy a new one each year because they look different. However, craft can inform mass production and vice versa.
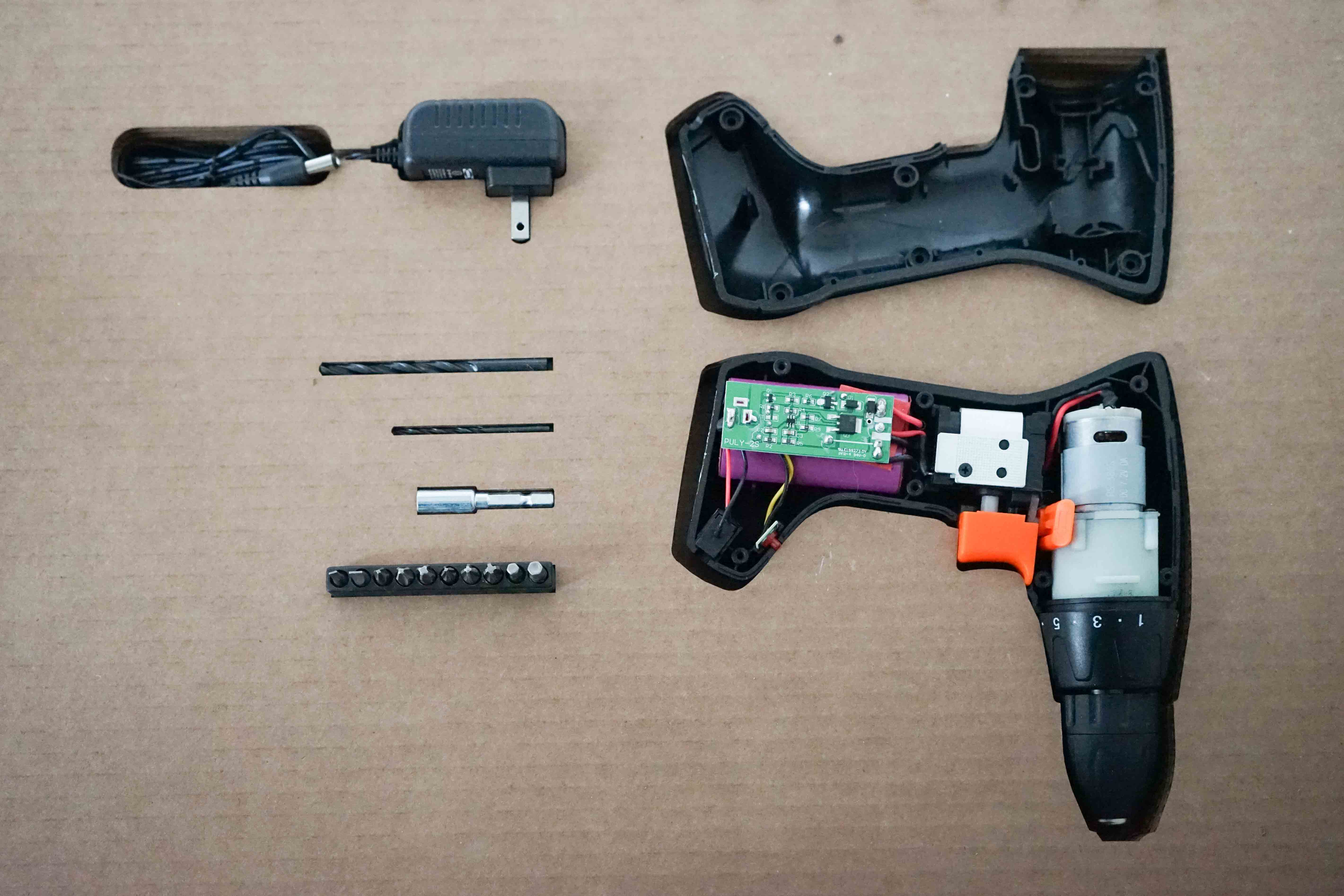
Before this thesis, did you know how these objects worked?
To some extent. I’ve always been taking things apart. Ever since I was a kid, I was interested in how things worked.
What’s the first thing that you’ve taken apart? Ever?
Ever? I have no idea. But the first thing I built was one of those bird house kits from Home Depot.
What led you into this interest?
My dad works in service and repair for quality control equipment and then my grandfather, even though he was a banker, always had a workshop in the basement. My other grandpa was interested in woodworking, so he’s the one who I built the birdhouse with. He built a lamp with me when I was little, or I watched him build a lamp. My dad’s uncle had a machine farm so I always had exposure. I’d walk in and see everything apart.
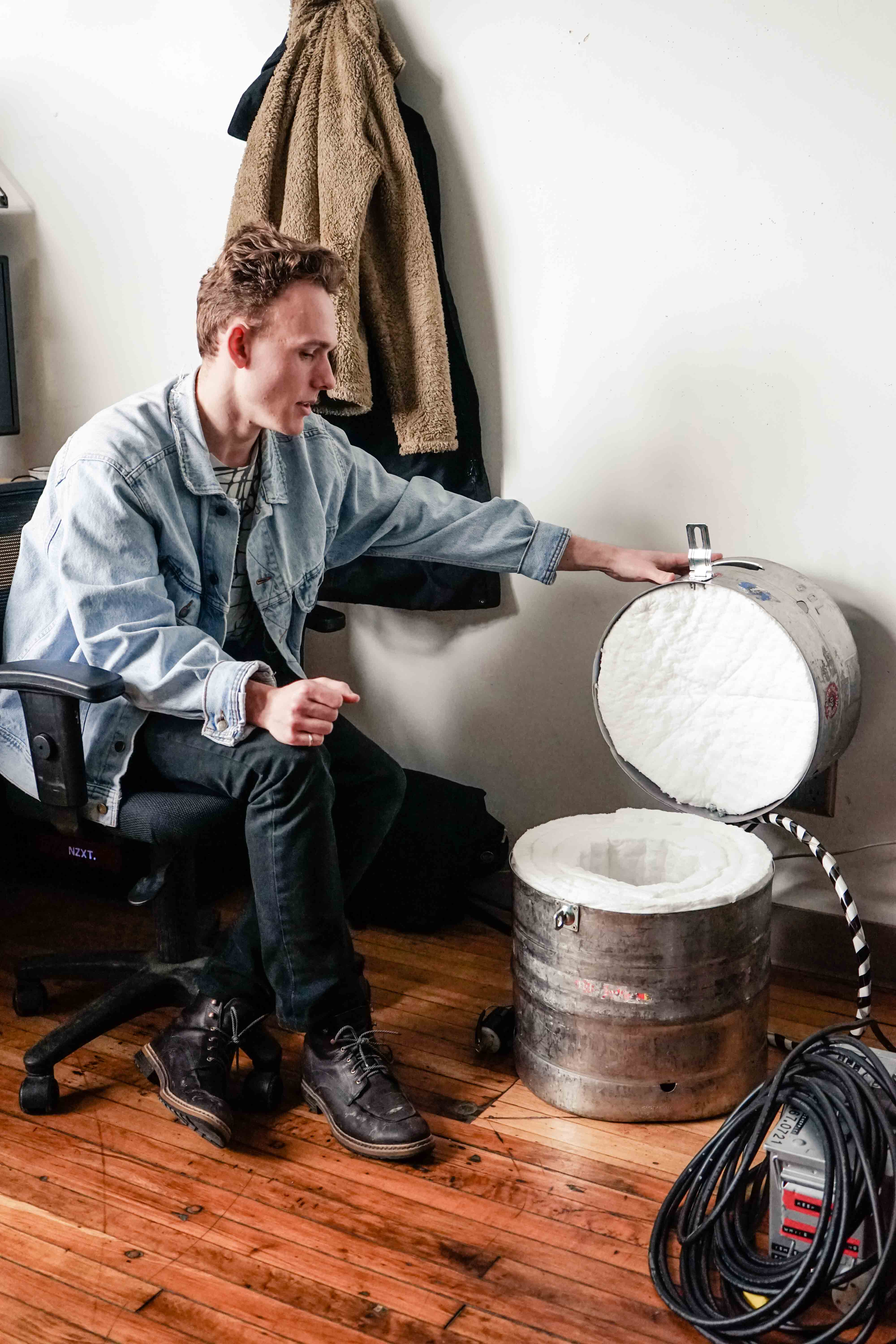
Can you tell us about the aluminum oven?
It’s got some insulation and you can check the temperature of the inside. Hopefully by the end I can melt some aluminum with it.
What are you going to do with melted aluminum?
So my supervisor Jane really wants to take apart some things and rebuild their broken parts with aluminum which is usually more durable than the material it was initially made out of. I also have some interest in some industrial design, so I want to cast simple products with it.
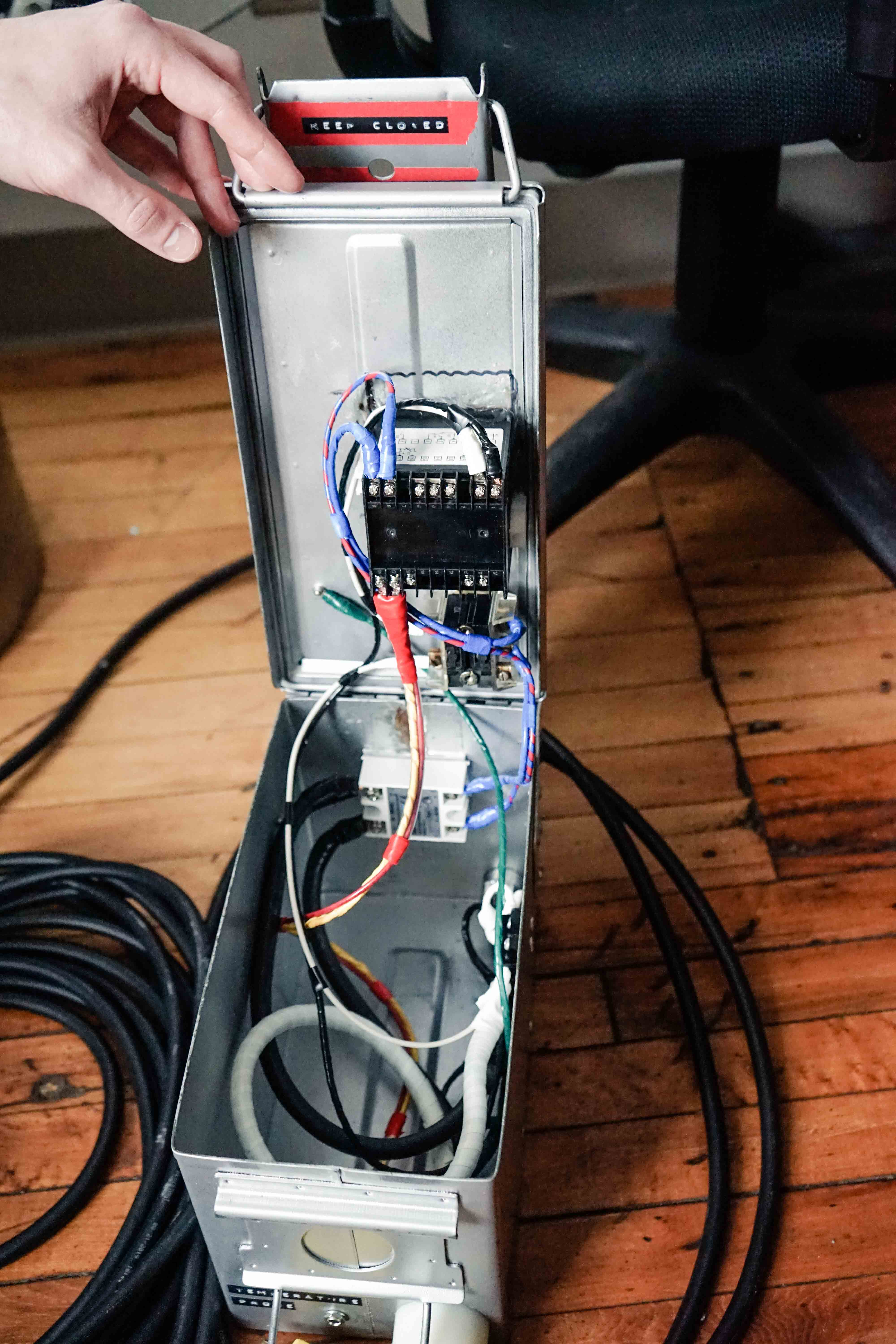
What are your main resources for how to make these things?
For electrical, my dad’s always been a good source since that’s what he works with. An awesome resource is Instructables, which is an online, do-it-yourself manual that was purchased by Autodesk almost ten years ago. People post what they’re working on so they have a huge variety of projects. They will also post extra tips on how to make something better. That site is probably my first exposure to projects that are more complicated than woodworking.
Do you have any experiences in product design?
I had some experience working for Phillip Beesley. That term I designed a lot of lighting fixtures that are held in Luddy Hall in Indiana and the ROM. I got to redesign a lot of components for laser cutting made of acrylic and stainless steel. That’s my main experience being in a rigorous industrial design environment. Other than that, it’s just side projects for fun.
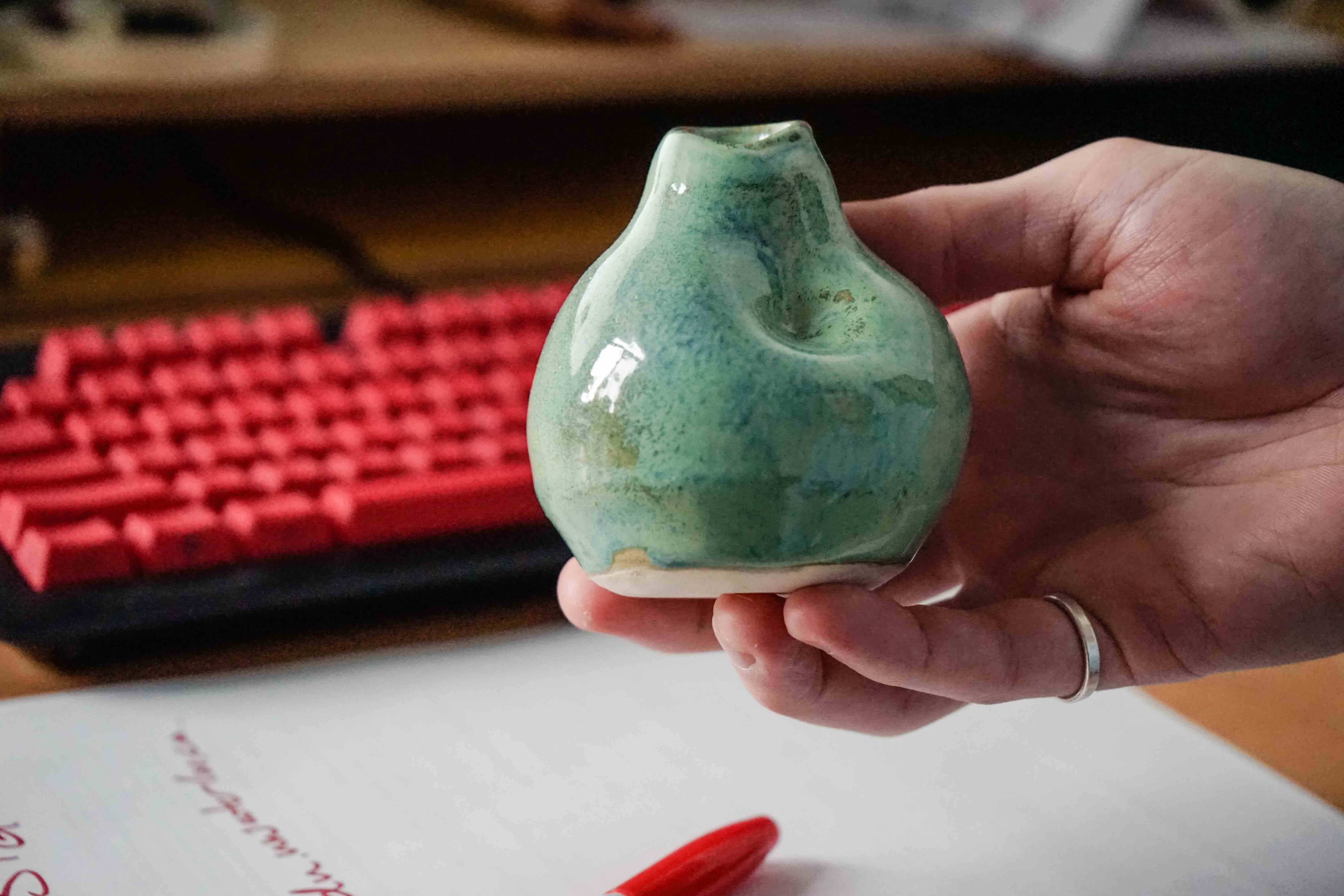
What kind of projects have you done?
Planters. I’m working on a comb. One is laser cut, the other one is in the finishing stages, so I’m playing around with sandblasting. The big jump for me is learning electropolishing which is finishing it to a mirror-like quality by putting it in acid and then using an electrical current to remove the outer layer of material.
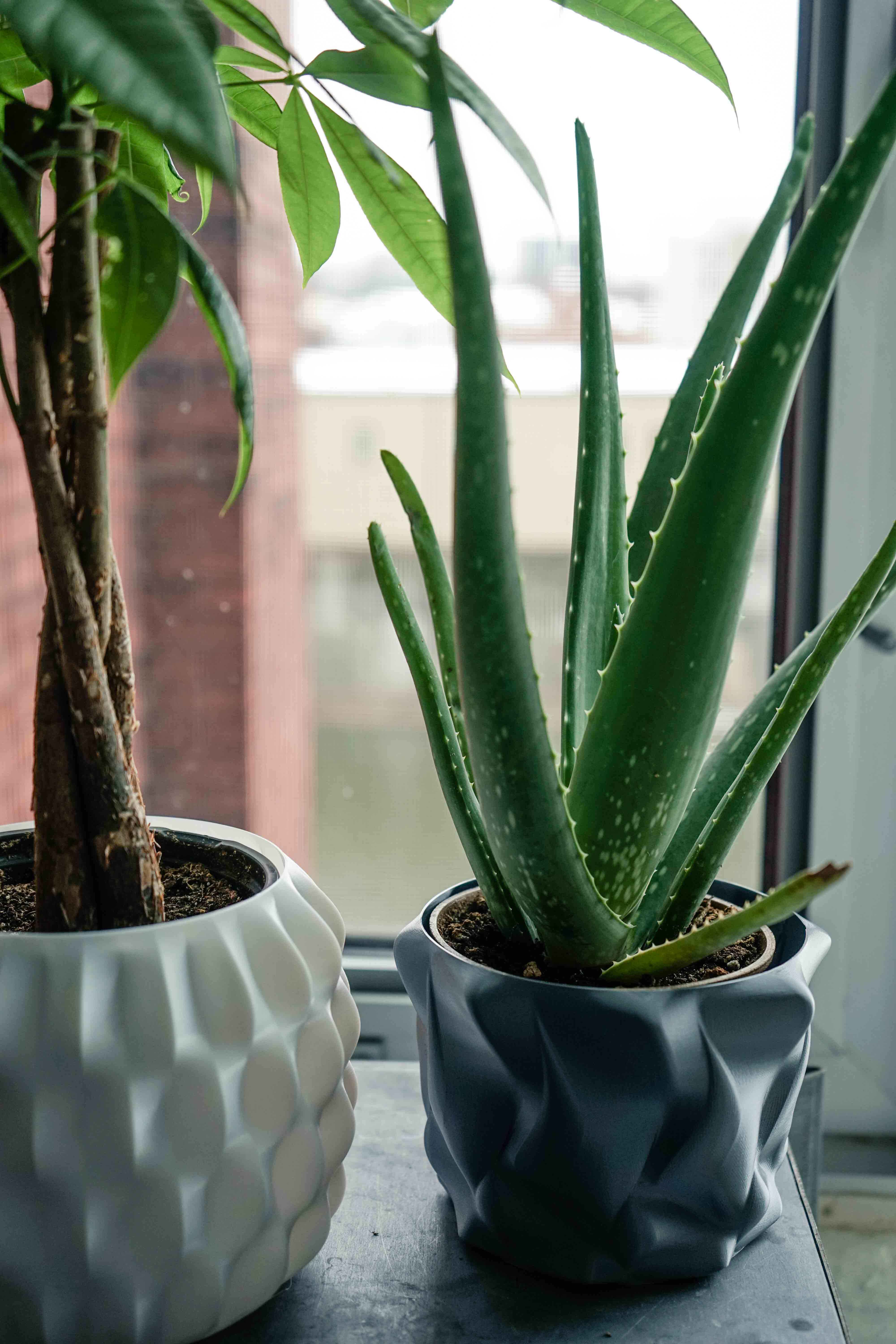
Is your design process mostly digital or do you do a lot of prototyping?
I do very little physical prototyping unless it’s for jigs that are part of the process but not the actual design item. For example, for the electropolishing process, I have to create a mounting system that keeps the objects suspended in the acid without touching the bottom or touching each other. When I’m designing an individual product, I like to have a good idea of what I’m aiming for, so I’ll make a sketch or a 3D model depending on how complicated it is.
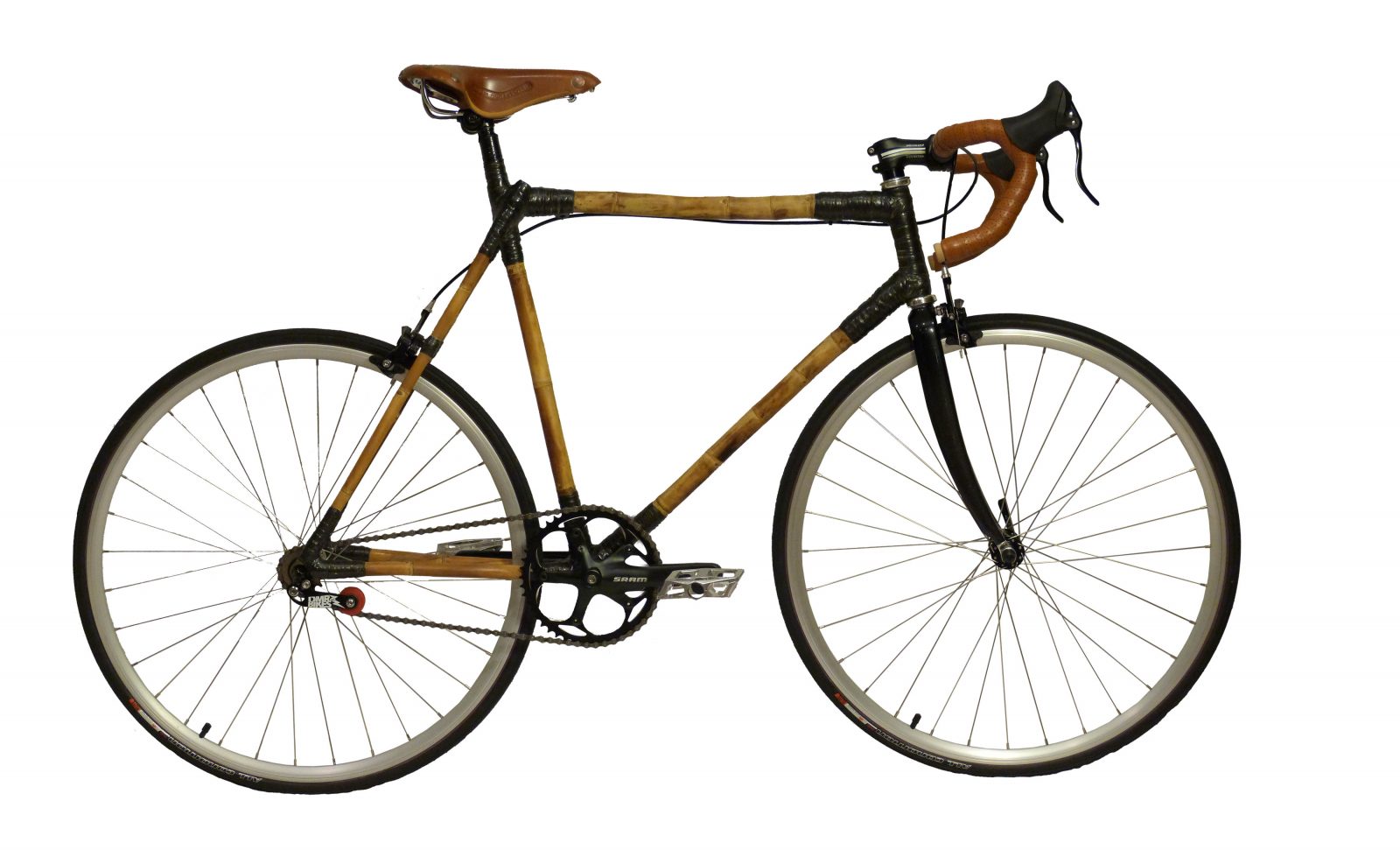
Can you tell us about the bike you brought into your interview?
This was a really fun project. A lot of the work was in building the jig. So the first step was building the jig that would hold the framed pieces together. That was its own project in itself. It’s important because it sets the angle of the geometry and lets you accurately build the frame to a particular dimension. I was working at a bike shop at the time so luckily I had a discount for many of the parts. I also had a coworker who was really nice to give me the carbon fiber fork and bearing system which saved a lot.
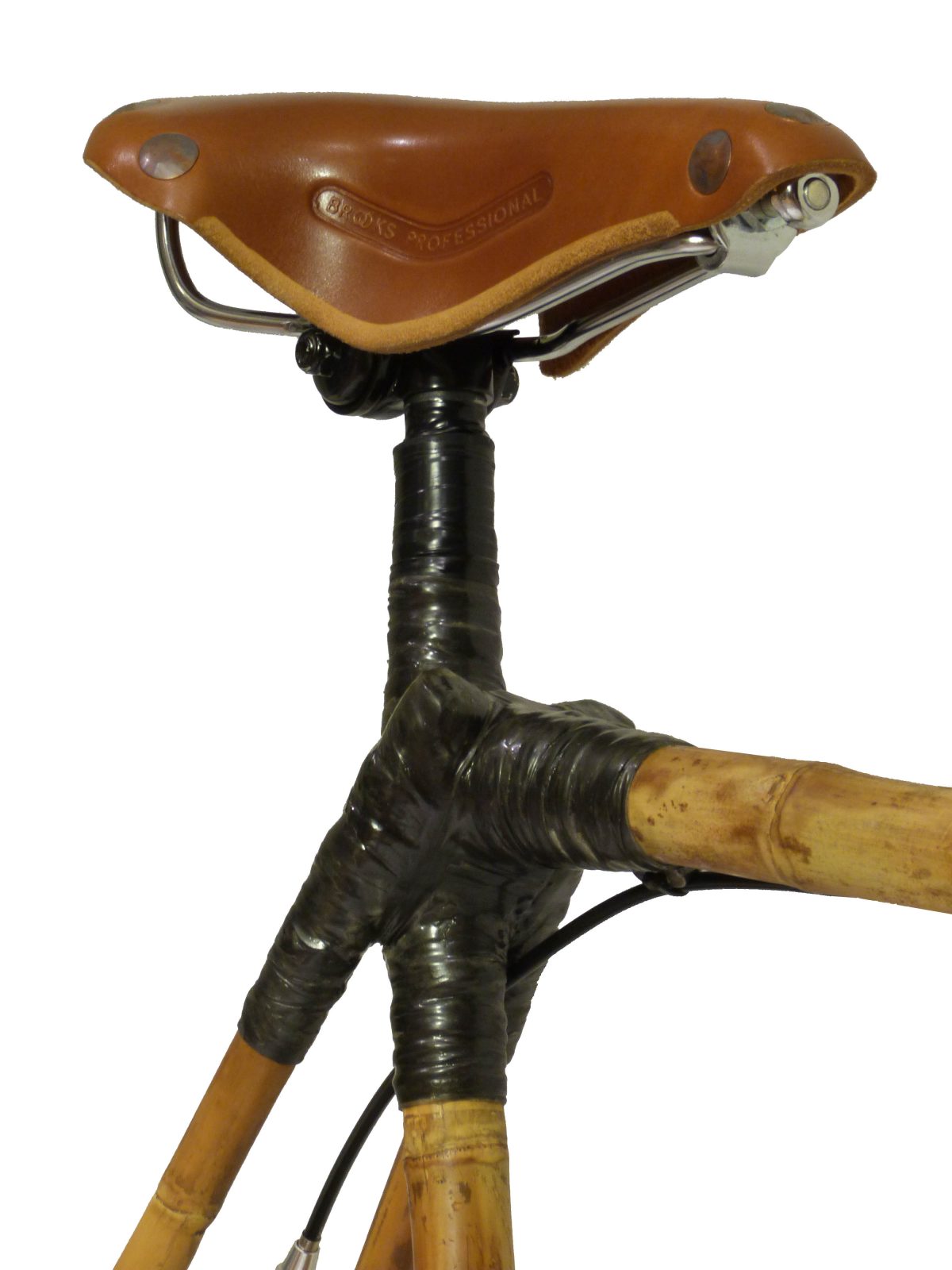
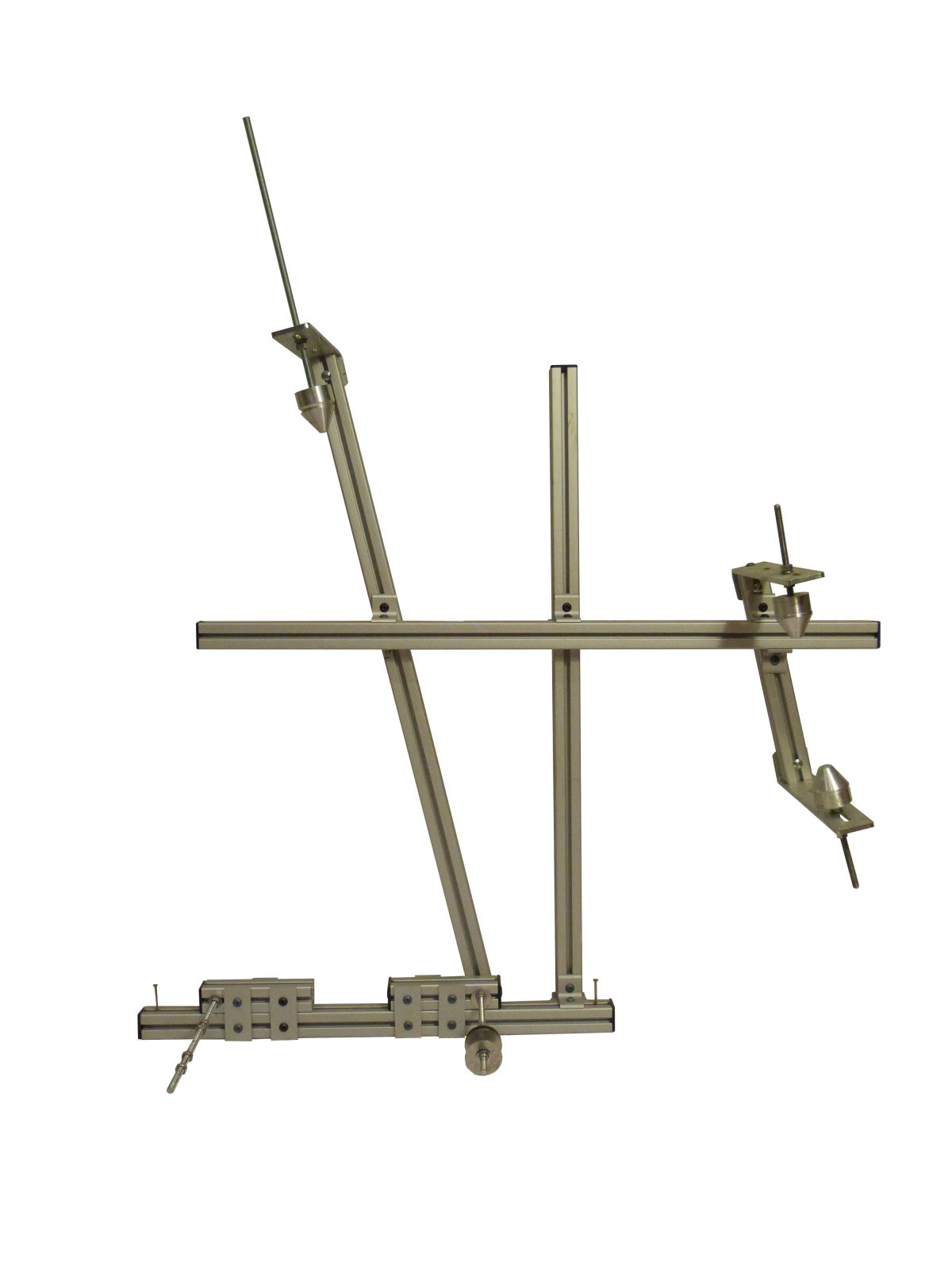
How much was everything?
With all the aluminum and buying more material than used, it was probably almost $1000. That cost includes the jig and some materials, like the extra carbon, that I’m still using today.
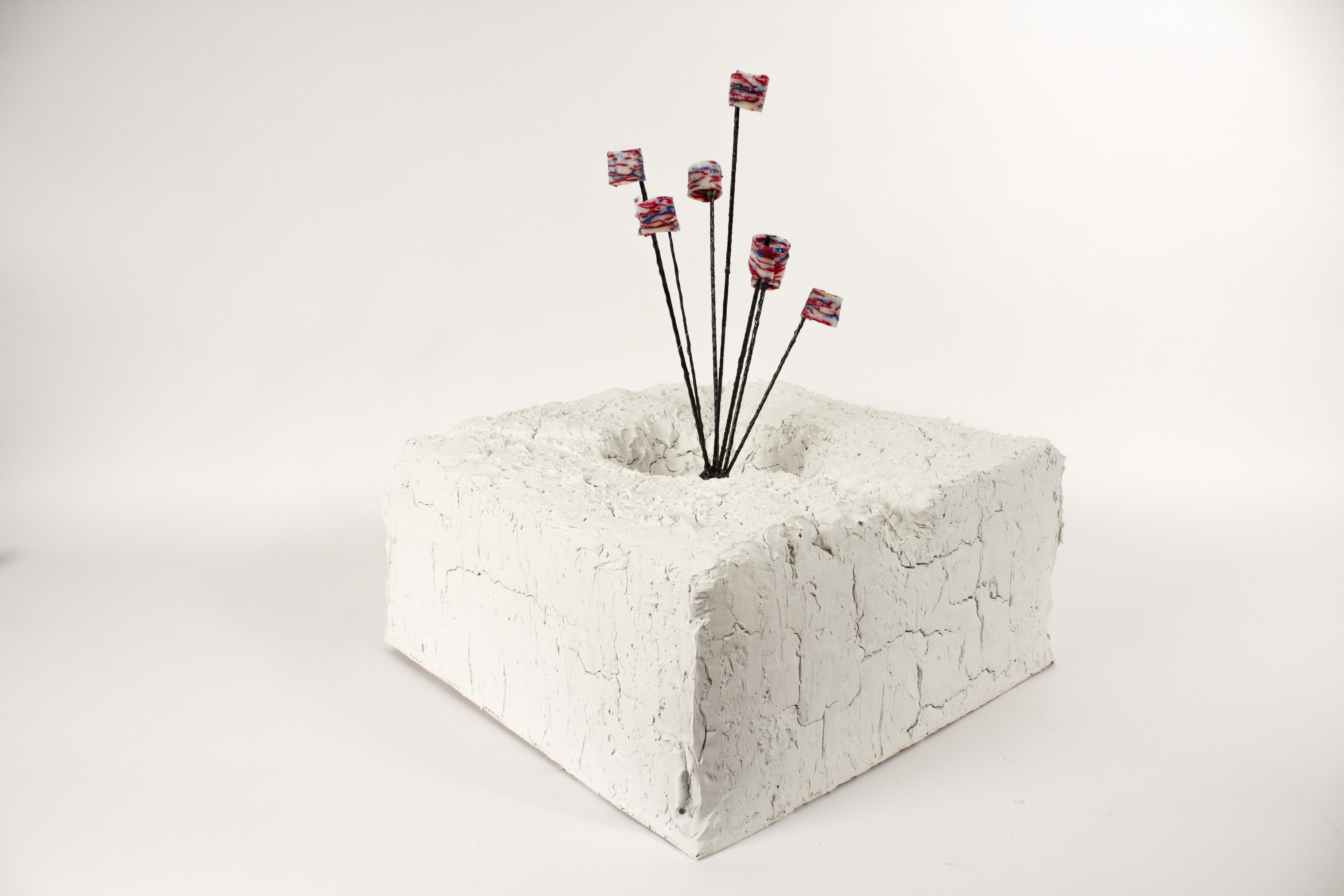
Do you tend to experiment a lot in your models?
During some projects that allow for experimentation, so during our 2B term with Scott Sorli, where we had to play with materials you could find at Home Depot.
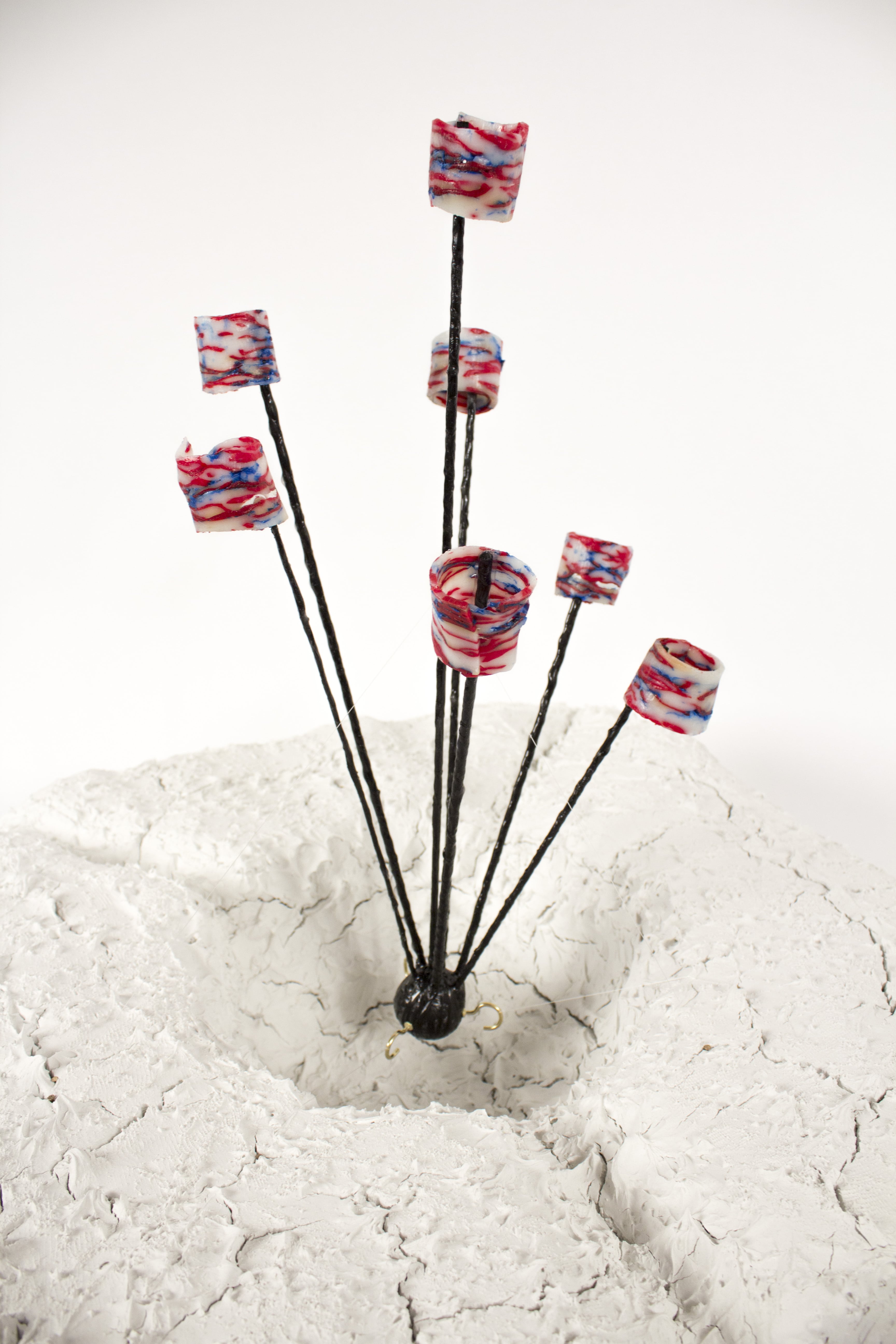
What’s your favourite material to work with?
I really like metals. They’re a little tough to start working with, since you need a little more planning, but I like the final quality that comes out. Other than that, wood and plastics are really nice. Wood is nice because you can go fast and figure things out as you go. Plastic is nice because if you’re making it yourself, you have a lot of control over what it looks like.
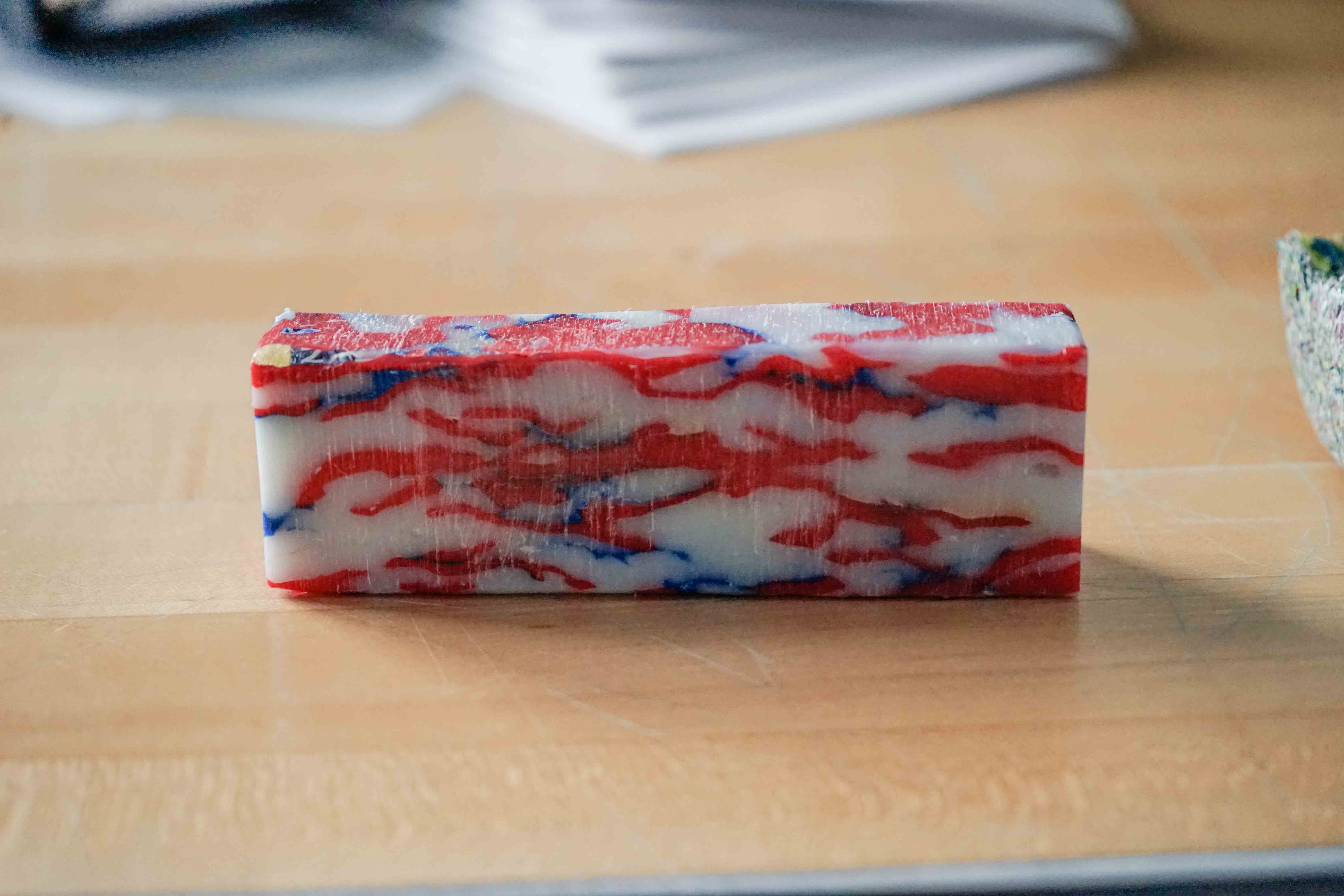
Who inspires you in your design work and what precedents do you look at?
I really like David Hakkens’ project with Precious Plastics and how he’s creating an open source tool set. There’s a couple of people on Youtube like Jimmy Diresta. Then there’s Adam Schwartzentruber from Boko, which is a design build practice that uses digital tools. I would also say my family members who’ve taught me things along the way.
Leave a Reply